Bonding process between metal substrate and glass substrate
A technology for metal substrates and glass substrates, applied in the direction of surface pretreatment bonding methods, adhesives, bonding methods, etc., can solve problems such as difficult cleaning, strong odor, and inability to meet the requirements of bonding strength, and achieve enhanced bonding Force, the effect of improving the connection strength
- Summary
- Abstract
- Description
- Claims
- Application Information
AI Technical Summary
Benefits of technology
Problems solved by technology
Method used
Image
Examples
preparation example Construction
[0025] The preparation process of the adhesive film can be as follows: Weigh the thermoplastic polyurethane resin, the latent curing agent, the thickener and other auxiliary agents according to the above formula, mix them evenly to obtain a water-dispersed mixture, and add a certain amount of deionized water to adjust. The value of the solids content of the water-dispersed mixture.
[0026] Then, the water-dispersed mixture is evenly coated on the release film or release paper, and after being baked in an oven for a period of time to be completely dried, an adhesive film with a certain thickness is obtained. In a specific embodiment, the temperature of the oven may be 50° C., and the drying time may be about 10 minutes.
[0027] Another embodiment of the present invention provides a bonding process between a metal substrate and a glass substrate, which utilizes the above-mentioned adhesive film. The bonding process includes the following steps:
[0028] S1. The surface of the m
Embodiment 1
[0039] Add 100 parts of Dispercoll U58, 8 parts of Dispercoll 2516, 1.5 parts of Rheovis PU 1190, 2 parts of DYNOL 604, 1 part of BYK 333 to a 250ml plasticizing cup, and add deionized water and mix well to obtain solid content The mixture was dispersed in 48 wt% water. The above-mentioned water-dispersed mixture was evenly coated on the PE coated release paper, baked in an oven at 50° C. for 10 minutes, and after it was completely dried, an adhesive film with a thickness of 100 μm was obtained.
[0040] Plasma sputtering was performed on the stainless steel surface using a jet AP plasma treatment system with a scan rate of 1 m / min. The polymer coating selects 94Prime from 3M Company as the polymer primer. The ink coating is made of HF GV3-S from Seiko Ink.
[0041] Place the adhesive film between the polymer coating and the ink coating, remove the PE-coated release paper, then press at 100°C and 0.4Mpa pressure for 60s, then take it out and let it stand for 4h.
Embodiment 2
[0043] Add 100 parts of Dispercoll 2899, 8 parts of Dispercoll 2516, 1.5 parts of Rheovis PU 1190, 2 parts of DYNOL 604, 1 part of BYK 333 to a 250ml plasticizing cup, and add deionized water and mix well to obtain solid content The mixture was dispersed in 48 wt% water. The above-mentioned water-dispersed mixture was evenly coated on the PE coated release paper, baked in an oven at 50° C. for 10 minutes, and after it was completely dried, an adhesive film with a thickness of 100 μm was obtained.
[0044] Plasma sputtering was performed on the stainless steel surface using a jet AP plasma treatment system with a scan rate of 1 m / min. The polymer coating selects 94Prime from 3M Company as the primer. The ink coating is made of HF GV3-S from Seiko Ink.
[0045] Place the adhesive film between the polymer coating and the ink coating, remove the PE-coated release paper, then press at 100°C and 0.4Mpa pressure for 60s, then take it out and let it stand for 4h.
PUM
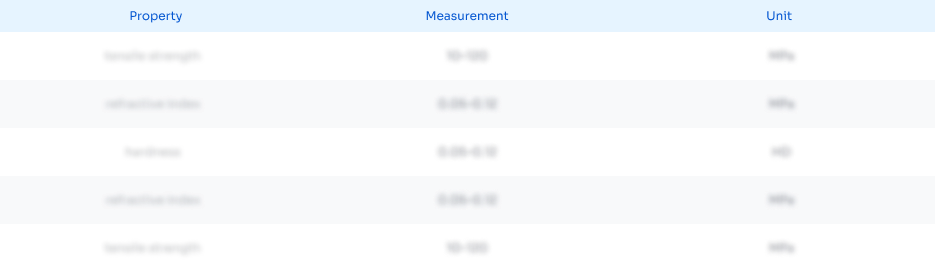
Abstract
Description
Claims
Application Information
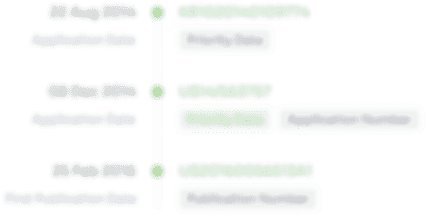
- R&D Engineer
- R&D Manager
- IP Professional
- Industry Leading Data Capabilities
- Powerful AI technology
- Patent DNA Extraction
Browse by: Latest US Patents, China's latest patents, Technical Efficacy Thesaurus, Application Domain, Technology Topic.
© 2024 PatSnap. All rights reserved.Legal|Privacy policy|Modern Slavery Act Transparency Statement|Sitemap