Process for full water phase synthesis of pharmaceutical intermediate dimethyl cyanoiminodithio-carbonate
A technology of dimethyl carbamate and dimethyl carbamate, which is applied in the field of all-water phase synthesis of pharmaceutical intermediate dimethyl carbamate, which can solve the problems of high pressure resistance, dangerous operation and low yield. problems, to achieve the effects of mild reaction conditions, reduced use, and reduced costs
- Summary
- Abstract
- Description
- Claims
- Application Information
AI Technical Summary
Problems solved by technology
Method used
Examples
Example Embodiment
[0020] Example 1:
[0021] The feed ratio (mole) is: calcium cyanamide: sodium carbonate: carbon disulfide = 1:1.02:1.2 in the first step, and calcium cyanamide: dimethyl sulfate = 1:2.2 in the second step.
[0022] In the first step, add 35g of industrial grade calcium cyanamide (containing 20% available nitrogen), 140ml of water, and then add 27g of sodium carbonate to mix in a three-necked flask with a stirrer, and add the catalyst cetyltrimethyl bromide 0.3g ammonium chloride, add 18.19mLCS dropwise 2 , Control the temperature at 40℃~43℃, stir the mixture until CS 2 All dissolved (about 4 hours). The mixture is filtered while hot without cooling, the filtrate is collected, and the filter residue is treated with 60 ml of water. The washing liquid is collected separately, and the washing liquid is used for the preparation of the next batch. The filtrate was directly used in the next methylation reaction.
[0023] In the second step, take the mother liquor of the disodium dibasic
Example Embodiment
[0024] Example 2:
[0025]The method is the same as in Example 1. The feed ratio (mole) is changed to the first step (calcium cyanamide: sodium carbonate: carbon disulfide = 1:1.02:1.2), and the second step (calcium cyanamide: dimethyl sulfate = 1: 2.1) The calcium cyanamide is still 35g, and the catalyst is changed to cetyltriethylammonium chloride.
[0026] In the first step, add 35g of commercial calcium cyanamide (industrial grade, 20% available nitrogen), 120ml of water, and then add 27g of sodium carbonate to mix in a three-necked flask with a stirrer, and add the catalyst cetyltrimethyl 0.3g ammonium bromide, add 18.19mLCS dropwise 2 , Control the temperature to 40℃~45℃, stir the mixture until CS 2 All dissolved (about 3 hours). The mixture is filtered while hot without cooling, the filtrate is collected, and the filter residue is treated with 60 ml of water. The washing liquid is collected separately, and the washing liquid is used for the preparation of the next batch. The f
Example Embodiment
[0028] Example 3:
[0029] The method is the same as in Example 1. The feed ratio (mole) is changed to the first step (calcium cyanamide: sodium carbonate: carbon disulfide = 1:1: 1.1), and the second step (calcium cyanamide: dimethyl sulfate = 1: 2.0), the calcium cyanamide is 35g, and the catalyst is changed to phenyltrimethylammonium chloride.
[0030] In the first step, add 35g of commercial calcium cyanamide (industrial grade, 20% available nitrogen), 160ml of water, add 26.5g of sodium carbonate to the three-necked flask with a stirrer, and add the catalyst cetyltrimethyl 0.3g ammonium bromide, add 16.6mLCS dropwise 2 , Control the temperature at 35℃~42℃, stir the mixture until CS 2 All dissolved (about 5 hours). The mixture is filtered while hot without cooling, the filtrate is collected, and the filter residue is treated with 60 ml of water. The lotion is collected separately and used for the next batch of preparation. The filtrate is directly used in the next methylation rea
PUM
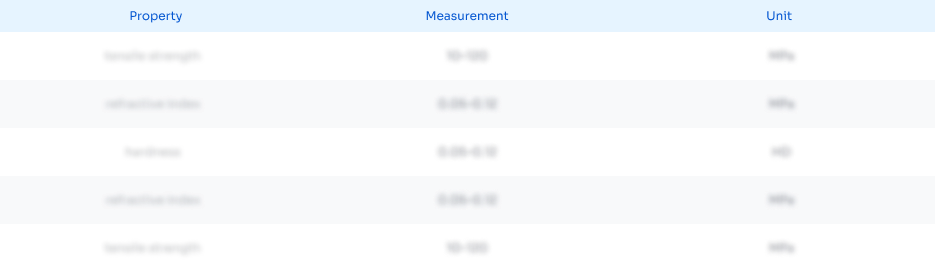
Abstract
Description
Claims
Application Information
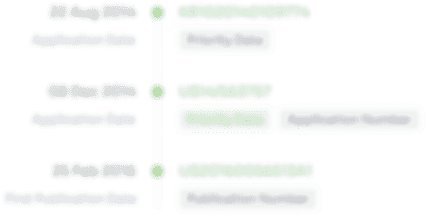
- R&D Engineer
- R&D Manager
- IP Professional
- Industry Leading Data Capabilities
- Powerful AI technology
- Patent DNA Extraction
Browse by: Latest US Patents, China's latest patents, Technical Efficacy Thesaurus, Application Domain, Technology Topic.
© 2024 PatSnap. All rights reserved.Legal|Privacy policy|Modern Slavery Act Transparency Statement|Sitemap