Contactor material for welding wire feeder
a feeder and contactor technology, applied in the direction of circuit-breaking switches, circuit-breaking switches for excess current, manufacturing tools, etc., can solve the problems of contactor performance degeneration, contactor ultimately overheating, and welds performed during the welding cycle may require extensive rewelding or other corrective measures
- Summary
- Abstract
- Description
- Claims
- Application Information
AI Technical Summary
Benefits of technology
Problems solved by technology
Method used
Image
Examples
Embodiment Construction
[0015] In the welding industry, a common product is an arc welder 10, as shown in FIG. 1 and schematically illustrated as including power source 20 with leads 22, 24. Wire feeder 30 enclosed in cabinet 32 has an internal electromechanical contactor 34 and a common ground 36. The wire feeder has an output welding lead 40 and a motor 50 operated at a speed determined by the signal on control line 52 from an internal microprocessor of the wire feeder. Motor 50 drives feed rolls 60, 62 through a shaft 64 to pull welding wire W from a supply, illustrated as reel or spool 70. The welding wire is moved through an electrical contact tip 72 located in welding gun 80 to direct electrode E toward workpiece WP for performing an electric arc welding process. The electrical circuit is completed by ground lead 82 attached to workpiece WP, in accordance with standard welding technology. In operation, contactor 34 is closed when a trigger switch within gun 80 is closed by an operator to drive wire W in
PUM
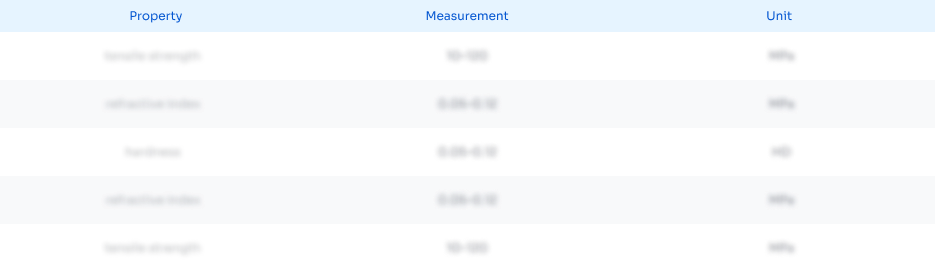
Abstract
Description
Claims
Application Information
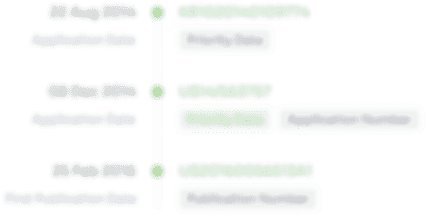
- R&D Engineer
- R&D Manager
- IP Professional
- Industry Leading Data Capabilities
- Powerful AI technology
- Patent DNA Extraction
Browse by: Latest US Patents, China's latest patents, Technical Efficacy Thesaurus, Application Domain, Technology Topic.
© 2024 PatSnap. All rights reserved.Legal|Privacy policy|Modern Slavery Act Transparency Statement|Sitemap