Laminates and methods of making same
a technology of laminates and optical films, applied in the field of laminates, can solve the problems of aesthetic defects, adversely affecting the optical performance of the film, and and achieve the effects of reducing the occurrence or degree of delamination, preventing edge delamination of the optical film, and reducing the problem of edge delamination
- Summary
- Abstract
- Description
- Claims
- Application Information
AI Technical Summary
Benefits of technology
Problems solved by technology
Method used
Image
Examples
examples
[0072] In making exemplary glazing laminates according to the present invention the following items can be used:
TYZOR ™ TPTA tetraisopropyl titanate (TPT) primer,available from E.I. DuPontdeNemours & Co. (Wilmington, DE)SAFLEX AR 110.38 mm polyvinyl butyral (PVB) available fromSolutia Inc., (St. Louis, MO)SRFSolar Reflecting Film (SRF), a multi-layer optical filmmade by Minnesota Mining and ManufacturingCompany.*AutoclaveScholz Maschinenbau GmbH & Co. KG (Coesfeld,Germany) or Melco Steel Inc. (Azusa, California)
*In accordance with the teachings, for example, of one or more of U.S. Patents Nos. 5,360,659 and 6,157,490, and PCT Publications Nos. WO 99 / 36248, WO 01 / 96104, and WO 02 / 061469.
[0073] Typically, the PVB does not become sufficiently transparent until after being heated to the point of fully bonding to the SRF and its corresponding glazing component. In addition, each pair of glazing components used to make a windshield were made of glass and generally equal in size (i.e
PUM
Property | Measurement | Unit |
---|---|---|
Depth | aaaaa | aaaaa |
Optical properties | aaaaa | aaaaa |
Abstract
Description
Claims
Application Information
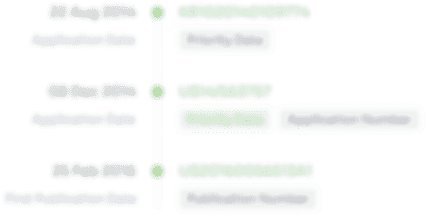
- R&D Engineer
- R&D Manager
- IP Professional
- Industry Leading Data Capabilities
- Powerful AI technology
- Patent DNA Extraction
Browse by: Latest US Patents, China's latest patents, Technical Efficacy Thesaurus, Application Domain, Technology Topic.
© 2024 PatSnap. All rights reserved.Legal|Privacy policy|Modern Slavery Act Transparency Statement|Sitemap