Continuous process for producing titanium tetrachloride
a technology of titanium tetrachloride and process, which is applied in the direction of titanium halides, chemistry apparatus and processes, inorganic chemistry, etc., can solve the problems of unwanted colored species in the product titanium dioxide pigment formation
- Summary
- Abstract
- Description
- Claims
- Application Information
AI Technical Summary
Benefits of technology
Problems solved by technology
Method used
Examples
example 1
Titanium Tetrachloride Purification Procedure
[0021]The effluent from a chlorinator reactor (50-60 wt. % TiCl4, 1000-3000 ppm VOCl3, 40-50 wt. % others, including impurity metal chlorides, unreacted ore and coke, and non-condensable gases) is cooled by passing the effluent into a cyclone. The chlorinator effluent is cooled to a temperature within a range of 180-300° C. The cyclone is cooled by a TiCl4 spray. The solid and liquid waste (containing unreacted ore and coke, ferrous chloride, manganese chloride, magnesium chloride, and chromium chloride) is separated from the vapor product, and the vapor product is taken overhead in the cyclone and passed to a first stage quench tower maintained at a temperature of from 60-90° C. The majority of TiCl4 is condensed in the tower and passed to a surge tank. Any vapor phase TiCl4 is passed to a second and third stage condenser which condenses the remaining TiCl4 and passes it to a crude TiCl4 tank. As the surge tank is filled, it overflows into
example 2
Vanadium Oxychloride Conversion
[0023]Analytical grade vanadyl trichloride (VOCl3, 0.96 g) is added to pure TiCl4 (683 g) in a 3-necked flask containing a magnetic stir bar, resulting in a TiCl4 solution containing 1406 ppm VOCl3. The flask is fitted with a thermometer connected to a calcium chloride drying tube, a polytetrafluoroethylene plastic gland with a rubber septum through which reactants can be added and samples withdrawn, and a second polytetrafluoroethylene plastic gland with a rubber septum through which two Teflon tubes are fit to circulate the reaction mixture to a flowcell of a FTIR (ASI, Columbia, Md.). The reaction mixture is circulated through the FTIR flowcell while being heated to 100° C. by a heating mantle. When the temperature stabilizes, Hyprene L1200 (950 microliters) is added to the mixture under agitation. Gradual decrease of VOCl3 peak at 1034 cm−1 is observed. After 257 minutes, a 10-mL sample is withdrawn via syringe through the septum. The sample is transf
example 3
Vanadium Oxychloride Conversion in the Presence of Aluminum Chloride
[0024]The procedure of Example 2 is repeated with the exception that analytical grade aluminum trichloride (3.38 g) is additionally added with VOCl3 (0.915 g) to pure TiCl4 (724 g), resulting in a TiCl4 solution containing 1264 ppm VOCl3. Also, only 550 microliters of Hyprene L1200 is added to the mixture under agitation.
[0025]In the presence of aluminum trichloride, the VOCl3 peak at 1034 cm−1 is immediately reduced. After 60 minutes, a 10-mL sample is withdrawn via syringe through the septum. The sample is transferred to a dry centrifuge tube and centrifuged. A sample of the clear liquid is analyzed to show ≦10 ppm V.
[0026]This example shows that the presence of aluminum trichloride aids the reduction of vanadium content in a TiCl4 solution. The amount of the Hyprene vanadium treatment agent is reduced by almost half compared to Example 2, yet the reaction rate has increased significantly resulting in appreciably low
PUM
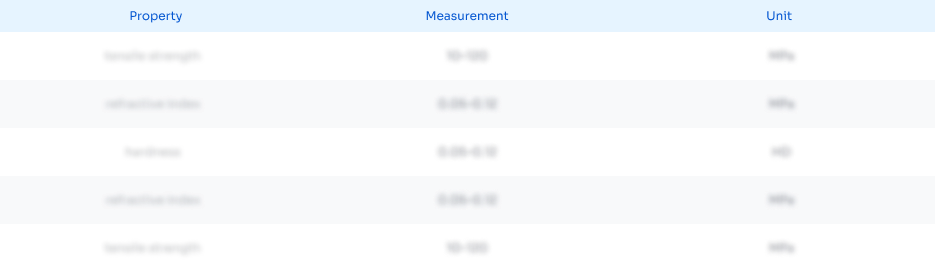
Abstract
Description
Claims
Application Information
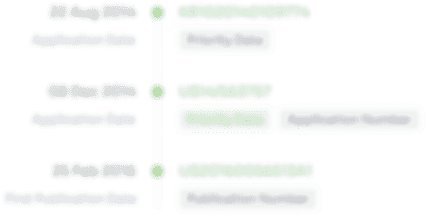
- R&D Engineer
- R&D Manager
- IP Professional
- Industry Leading Data Capabilities
- Powerful AI technology
- Patent DNA Extraction
Browse by: Latest US Patents, China's latest patents, Technical Efficacy Thesaurus, Application Domain, Technology Topic.
© 2024 PatSnap. All rights reserved.Legal|Privacy policy|Modern Slavery Act Transparency Statement|Sitemap