Integrally Molded Body of Silicone Resin and Silicone Rubber, Method of Manufacture, and Curable Silicone Resin Composition
a technology of silicone resin and integral body, which is applied in the field of integrally molded body of silicone resin and silicone rubber, and the method of manufacturing the integrally molded body, can solve the problems of silicone rubber and silicone resin adhesion, and the molding of silicone rubber and silicone resin into an integral body
- Summary
- Abstract
- Description
- Claims
- Application Information
AI Technical Summary
Benefits of technology
Problems solved by technology
Method used
Examples
example 1
Practical Example 1
[0077]A curable silicone resin composition (R1) was prepared by combining (i) a mixture composed of 84 gram of polyphenylmethylvinylsiloxane resin having a weight-average molecular weight of 1,600, and represented by the average molecular formula (PhSiO3 / 2)7(ViMe2SiO1 / 2)3, and 16 grain of polyphenylmethylvinylsiloxane resin having a weight-average molecular weight of 408, and represented by the average molecular formula (PhSiO3 / 2)(ViMe2SiO1 / 2)3; (ii) a mixture composed of 84 gram of polyphenylmethyl-hydrogensiloxane having a weight-average molecular weight of 1,100, and represented by the average molecular formula (PhSiO3 / 2)6 (HMe2SiO1 / 2)4, and 0.17 gram of 1-ethynyl-1-cyclohexanol.
[0078]This mixture was further combined with 0.017 gram of a complex of platinum and 1,3-divinyl-1, 1,3,3-tetramethyldisiloxane containing 4 weight percent of metallic platinum. In curable silicone resin composition (R1), the ratio of the mole number of silicon-bonded hydrogen
example 2
Practical Example 2
[0082]A curable silicone resin composition (R2) was prepared by combining (i) a mixture composed of 77 gram of polyphenylmethylvinylsiloxane resin having a weight-average molecular weight of 1,600, and represented by the average molecular formula (PhSiO3 / 2)7(ViMe2SiO1 / 2)3, and 23 gram of polyphenylmethylvinylsiloxane resin having a weight-average molecular weight of 408, and represented by the average molecular formula (PhSiO3 / 2)(ViMe2SiO1 / 2)3; (ii) a mixture composed of 75 gram of polyphenylmethylhydrogensiloxane having a weight-average molecular weight of 1,100, and represented by the average molecular formula (PhSiO3 / 2)6(HMe2SiO1 / 2)4, and 0.21 gram of 1-ethynyl-1-cyclohexanol. This mixture was combined with 0.016 gram of a complex of platinum and 1,3-divinyl-1,1,3,3-tetramethyldisiloxane containing 4 weight percent of metallic platinum. The ratio of the mole number of silicon-bonded hydrogen atoms to the mole number of vinyl groups in the curable silic
example 3
Practical Example 3
[0084]1,720 gram of the silicone rubber base prepared in Practical Example 1 were combined with 16 gram a methylhydrogensiloxane-dimethylsiloxane copolymer capped at both molecular terminals with trimethylsiloxy groups, and having the average molecular formula Me3SiO(MeHSiO2 / 2)3(Me2SiO2 / 2)3SiMe3, and 3.5 gram of a polymethylhydrogensiloxane capped at both molecular terminals with trimethylsiloxy groups, and having a viscosity of 20 mPa·s. The components were mixed in a two-roll mill, combined, and kneaded with 1.5 gram of 1-ethynyl-1-cyclohexanol, and 0.15 gram of a complex of platinum and 1,3-divinyl-1,1,3,3-tetramethyldisiloxane containing 4 weight percent of metallic platinum. A silicone rubber composition (E2) was obtained with a ratio of the mole number of silicon-bonded hydrogen atoms to the mole number of vinyl groups of 2.9.
[0085]A metal mold was loaded with equal half-quantities of the curable silicone resin composition (R1) prepared in Practical Example
PUM
Property | Measurement | Unit |
---|---|---|
Temperature | aaaaa | aaaaa |
Percent by mass | aaaaa | aaaaa |
Fraction | aaaaa | aaaaa |
Abstract
Description
Claims
Application Information
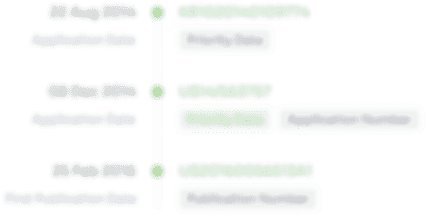
- R&D Engineer
- R&D Manager
- IP Professional
- Industry Leading Data Capabilities
- Powerful AI technology
- Patent DNA Extraction
Browse by: Latest US Patents, China's latest patents, Technical Efficacy Thesaurus, Application Domain, Technology Topic.
© 2024 PatSnap. All rights reserved.Legal|Privacy policy|Modern Slavery Act Transparency Statement|Sitemap