Self-compensating filament tension control device with eddy current braking
a tension control device and self-compensation technology, applied in the direction of filament handling, thin material processing, transportation and packaging, etc., can solve the problems of unfavorable use of tension control devices, and often multiple individual adjustments of creels having variable tension control
- Summary
- Abstract
- Description
- Claims
- Application Information
AI Technical Summary
Benefits of technology
Problems solved by technology
Method used
Image
Examples
Embodiment Construction
[0025]An exemplary self-compensating filament tension control device with eddy current braking according to the concepts of the present invention is generally indicated by the numeral 20 as seen in FIGS. 1-5. The tension control device 20 includes a fixed support 22 that is affixed to or is part of a creel or other support structure which is part of a machine that processes individual strands of filamentary material into a finished manufactured item. It will be appreciated that the creel likely supports multiple devices 20 as needed. The fixed support 22 includes a support frame 24 which is mounted on the creel via bolts, welding or other secure attachment. The support frame 24 includes at least two support arms 26 extending substantially perpendicularly therefrom and wherein the support arms 26 are utilized to support or carry other components of the control device 20. The support arms 26 are further identified as an upper support arm 26A and a lower support arm 26B.
[0026]The fixed su
PUM
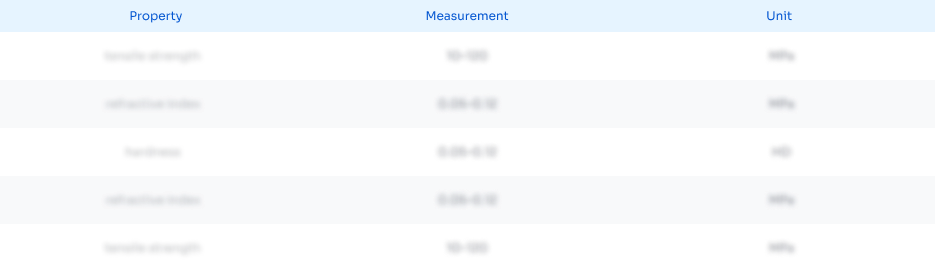
Abstract
Description
Claims
Application Information
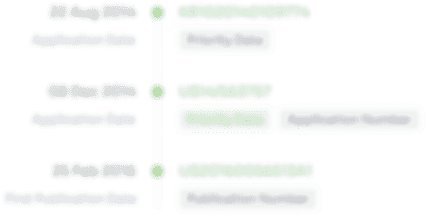
- R&D Engineer
- R&D Manager
- IP Professional
- Industry Leading Data Capabilities
- Powerful AI technology
- Patent DNA Extraction
Browse by: Latest US Patents, China's latest patents, Technical Efficacy Thesaurus, Application Domain, Technology Topic.
© 2024 PatSnap. All rights reserved.Legal|Privacy policy|Modern Slavery Act Transparency Statement|Sitemap