Capacitive touch panel
- Summary
- Abstract
- Description
- Claims
- Application Information
AI Technical Summary
Benefits of technology
Problems solved by technology
Method used
Image
Examples
first embodiment
[0044]In the first embodiment relative to the capacitive touch panel 100, the second sensing electrode serials 150 are disposed in a second direction on the top surface of the second transparent substrate 140. Each second sensing electrode serial 150 is formed by cascading second sensing electrodes 152, each of which substantially has a diamond shape. The second sensing electrode serials 150 are made of transparent conductive materials, such as ITO (Indium Tin Oxide), AZO (Aluminum-doped Zinc Oxide), IZO (Indium Zinc Oxide), nanosilver films, CNT (Carbon Nanotube), or graphene films. The second sensing electrode serials 150 are formed on the surface of the second transparent substrate 140 through etching, printing, or sputtering processes. Each second hollow region 154 is formed between two adjacent second sensing electrodes 152. The second direction is perpendicular to the aforementioned first direction.
[0045]FIG. 4A is a diagram for illustrating a sectional view of the capacitive tou
fifth embodiment
[0051]In the fifth embodiment relative to the capacitive touch panel 500, the second sensing electrode serials 550 are disposed in a second direction on the top surface of the second transparent substrate 540. Each second sensing electrode serial 550 is formed by cascading second sensing electrodes 552, each of which substantially has a diamond shape. The second sensing electrode serials 550 are made of transparent conductive materials, such as ITO (Indium Tin Oxide), AZO (Aluminum-doped Zinc Oxide), IZO (Indium Zinc Oxide), nanosilver films, CNT (Carbon Nanotube), or graphene films. The second sensing electrode serials 550 are formed on the surface of the second transparent substrate 540 through etching, printing, or sputtering processes. Each second hollow region 554 is formed between two adjacent second sensing electrodes 552. The second direction is perpendicular to the aforementioned first direction.
[0052]Please further refer to FIG. 12A. FIG. 12A is a diagram for illustrating a s
PUM
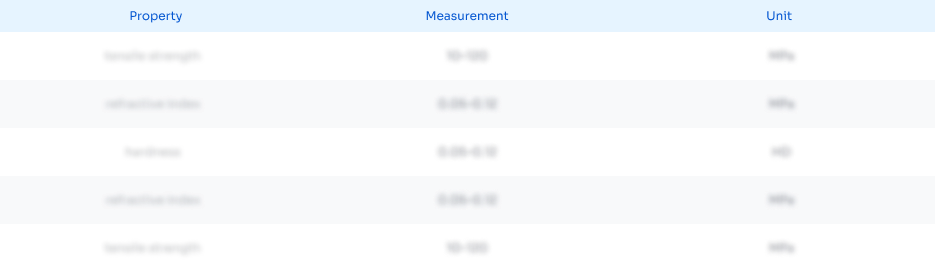
Abstract
Description
Claims
Application Information
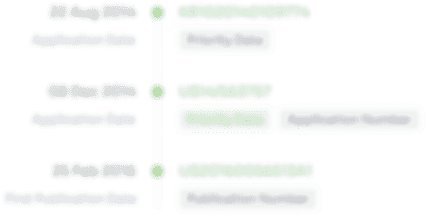
- R&D Engineer
- R&D Manager
- IP Professional
- Industry Leading Data Capabilities
- Powerful AI technology
- Patent DNA Extraction
Browse by: Latest US Patents, China's latest patents, Technical Efficacy Thesaurus, Application Domain, Technology Topic.
© 2024 PatSnap. All rights reserved.Legal|Privacy policy|Modern Slavery Act Transparency Statement|Sitemap