Fiber-reinforced resin laminate
- Summary
- Abstract
- Description
- Claims
- Application Information
AI Technical Summary
Benefits of technology
Problems solved by technology
Method used
Image
Examples
Example
Example 1
Production of Prepreg
[0151]Carbon fibers (manufactured by Mitsubishi Rayon Co., Ltd., product name: PYROFILL TR-50S15L) were aligned in a planar form such that the direction of the reinforcing fibers was unidirectional, and thus a reinforcing fiber sheet having a basis weight of 72.0 g / m2 was produced. Both surfaces of this reinforcing fiber sheet were interposed between films of nylon 6 (nylon 6; manufactured by Ube Industries, Ltd., product name: 1013B, melting point: 218° C., thickness: 40 μm), and the reinforcing fiber sheet was impregnated with the thermoplastic resin by passing the assembly several times between calendar rolls. Thus, a prepreg having a carbon fiber volume percentage content (Vf) of 34% and a thickness of 0.125 mm was obtained.
[0152](Production of Fiber-Reinforced Resin Laminate)
[0153]The prepreg thus obtained was cut into a size of 300 mm on each side, and incisions were inserted therein at a constant interval as indicated in Table 1, using a sample cu
Example
Example 2
[0156]A fiber-reinforced resin laminate was produced in the same manner as in Example 1, except that incision processing at an angle θ formed by an incision that cut the fibers and a reinforcing fiber of 30° was performed such that the carbon fibers had a constant length (average fiber length) L of 25.0 mm and an average cutting length l of 20 mm. An evaluation of the laminate was performed. The sum total of the cutting length, la, per 1 m2 of the PPG used at the surface layer at this time was 80 m.
Example
Example 3
[0157]A fiber-reinforced resin laminate was produced in the same manner as in Example 1, except that the PPG and a nylon 6 sheet (nylon 6; manufactured by Ube Industries, Ltd., product name: 1013B) having a thickness of 1 mm were superposed as indicated in Table 1, and an evaluation of the laminate was performed. The sum total of the cutting length, la, per 1 m2 of the PPG used at the surface layer at this time was 56.6 in.
PUM
Property | Measurement | Unit |
---|---|---|
Fraction | aaaaa | aaaaa |
Fraction | aaaaa | aaaaa |
Angle | aaaaa | aaaaa |
Abstract
Description
Claims
Application Information
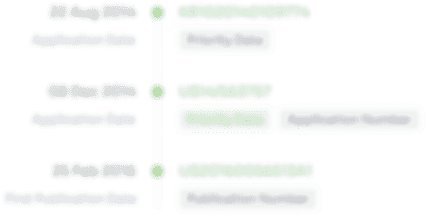
- R&D Engineer
- R&D Manager
- IP Professional
- Industry Leading Data Capabilities
- Powerful AI technology
- Patent DNA Extraction
Browse by: Latest US Patents, China's latest patents, Technical Efficacy Thesaurus, Application Domain, Technology Topic.
© 2024 PatSnap. All rights reserved.Legal|Privacy policy|Modern Slavery Act Transparency Statement|Sitemap