Plasma source utilizing a macro-particle reduction coating and method of using a plasma source utilizing a macro-particle reduction coating for deposition of thin film coatings and modification of surfaces
- Summary
- Abstract
- Description
- Claims
- Application Information
AI Technical Summary
Benefits of technology
Problems solved by technology
Method used
Image
Examples
Example
Example 1
Macro-Particle Reduction Coatings Reduce Macro-Particle Accumulation on a Substrate During Extended Plasma Source Operation
[0085]The inventors sought to determine the ability of the macro-particle reduction coatings of the instant invention to reduce macro-particle formation on a substrate during extended plasma source operation. A first test was performed using a hollow cathode plasma source comprising two uncoated stainless steel electrodes (“2kw Plain SS”). These electrodes were arranged substantially parallel to one another, and the distance between the centers of each hollow cathode cavity was 116 mm. The plasma length was 100 mm, measured along the length of each electrode, i.e. between the centers of the furthest plasma nozzles of each electrode. The plasma source was positioned over a ceramic substrate and used to generate a plasma for a run time of approximately 160 hours. This test was repeated with a separate uncoated stainless steel electrode under the same conditi
Example
Example 2
Macro-Particle Reduction Coatings Reduce the Formation of Macro-Particles in the Interior Cavity of Hollow Cathode Electrodes During Extended Plasma Source Operation
[0089]The inventors sought to determine the ability of the macro-particle reduction coatings of the instant invention to reduce macro-particle formation in the interior cavity of hollow cathode electrodes during extended plasma source operation.
[0090]FIG. 6 shows the results of an experiment wherein hollow cathode electrodes were provided and configured in a plasma source. The internal cavity of the hollow cathodes, where plasma formation occurs, was either uncoated (Plain SS), or was coated with a tungsten carbide coating (WC Coated). The coating was approximately 100 μm thick, and comprised a 12% cobalt binder. The plasma sources were used to generate a plasma for a predetermined period of time greater than 100 hours. Specifically, the predetermined period of time was between 100-200 hours. After completion of th
Example
Example 3
Macro-Particle Reduction Coatings Stabilize Voltage Output During Extended Plasma Source Operation
[0092]The inventors sought to determine the ability of the macro-particle reduction coatings of the instant invention to reduce voltage drift of a plasma source during extended operation.
[0093]Output voltage was compared between a hollow cathode plasma source incorporating uncoated stainless steel electrodes and a similar hollow cathode plasma source incorporating electrodes coated with a macro-particle reduction coating, during extended operation of the plasma sources.
[0094]In the first test, a hollow cathode plasma source comprising two uncoated stainless steel electrodes were used to generate a plasma for a test run lasting at least 144 hours, at a power density of 20 kW / m. As shown in FIG. 7A, the operating voltage increased by approximately 20 volts over the course of the test run. When the power was increased to 40 kw / m in a similar test, the voltage increased by approxi
PUM
Property | Measurement | Unit |
---|---|---|
Time | aaaaa | aaaaa |
Time | aaaaa | aaaaa |
Thickness | aaaaa | aaaaa |
Abstract
Description
Claims
Application Information
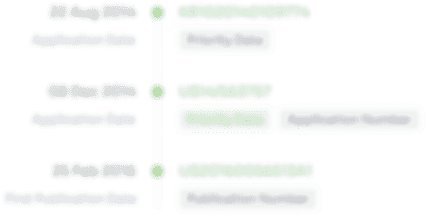
- R&D Engineer
- R&D Manager
- IP Professional
- Industry Leading Data Capabilities
- Powerful AI technology
- Patent DNA Extraction
Browse by: Latest US Patents, China's latest patents, Technical Efficacy Thesaurus, Application Domain, Technology Topic.
© 2024 PatSnap. All rights reserved.Legal|Privacy policy|Modern Slavery Act Transparency Statement|Sitemap