Improved resorbable polymer purification process
a technology of resorbable polymer and purification process, which is applied in the field of improved purification process of resorbable polymer, can solve the problems of high volume of chemical waste, limited industrial application of this synthetic route, and intoxication of surrounding tissue,
- Summary
- Abstract
- Description
- Claims
- Application Information
AI Technical Summary
Benefits of technology
Problems solved by technology
Method used
Image
Examples
example 1
y(D,L-Lactide-Co-Glycolide) (RESOMER® Select 7525 DLG 7E)
[0052]D,L-lactide and glycolide were polymerized in bulk catalyzed by tin 2-ethyl hexanoate and initiated by alcohol. The resulting poly(D,L-lactide-co-glycolide) with ester end group was characterized to have an averaged molecular weight (Mw) of 121 kDa, Mw / Mn of 1.6 by GPC, and residual tin content 90 ppm.
[0053]25 g of this polymer was dissolved in acetone to yield a 9-10 wt % solution. Activated carbon was added to absorb the residual Sn2+ in the polymer. The resulting suspension was stirred for 4 hours, filtered to remove activated carbon, followed by recovery of the purified polymer solid by anti-solvent precipitation with water. Different amounts of activated carbon used in the process yielded different residual Sn2+ content after separation and recovery, as shown in Table 1.
[0054]In entry 1-5, use of excess amounts of activated carbon was necessary to reach less than 1 ppm residual tin. The amount of carbon (25 wt %) is
example 2
Lactide) (RESOMER® Select 100 DL 12A)
[0055]D,L-lactide was polymerized in bulk catalyzed by tin 2-ethyl hexanoate and initiated by glycolic acid. The resulting poly(D,L-lactide) with acid end group was characterized to have an average molecular weight (Mw) of 186 kDa, Mw / Mn of 1.7 by GPC, and tin content of 89 ppm.
[0056]12.5 g poly(D,L-lactide) was dissolved in 250 mL acetone to yield a clear amber solution. A combination of activated carbon and lactic acid was added to remove the residual Sn2+ in the polymer. The resulting suspension is stirred for 3 hours, filtered to remove activated carbon, followed by recovery of the purified polymer solid by anti-solvent precipitation with water. Different amounts of activated carbon and lactic acid produced purified polymer with different residual Sn2+ contents as shown in Table 2.
[0057]The addition of lactic acid boosted the activated carbon tin removal efficiency. The amount of activated carbon can be reduced to as low as 1 wt % when using 3
example 3 (
Thermal Stability)
[0060]Polymer thermal stability is an important parameter during the dry formulation processing, e.g. hot melt extrusion. It was reported that moisture, hydrolyzed monomers and oligomers, and residual metals are key factors that influence poly(D,L-lactide) thermal stability (D. Cam et al Polymer 38, 1997, 1879-1884). Poly(D,L-lactide) with an IV of 1.2 dL / g is processed via four different methods to give four products with different amounts of residual tin and residual monomer contents. The analytical results of these processed poly(D,L-lactide)s are listed in Table 3. The thermal stability of these polymers was studied by holding them at 230° C. over 2 h under nitrogen protection. Aliquots were taken at different time points and their weight-averaged molecular weights were characterized by GPC, as shown in FIG. 1.
TABLE 3Analytical data of poly(D,L-lactide)sobtained from different processesPolymerTinMonomerMWEntrydescription(ppm)(wt %)(kDa)1Base892.72032Low tin1.22.
PUM
Property | Measurement | Unit |
---|---|---|
Fraction | aaaaa | aaaaa |
Time | aaaaa | aaaaa |
Atomic weight | aaaaa | aaaaa |
Abstract
Description
Claims
Application Information
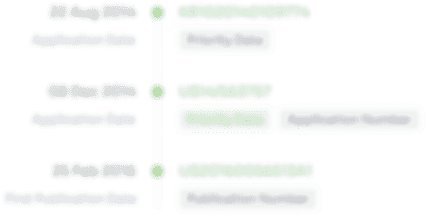
- R&D Engineer
- R&D Manager
- IP Professional
- Industry Leading Data Capabilities
- Powerful AI technology
- Patent DNA Extraction
Browse by: Latest US Patents, China's latest patents, Technical Efficacy Thesaurus, Application Domain, Technology Topic.
© 2024 PatSnap. All rights reserved.Legal|Privacy policy|Modern Slavery Act Transparency Statement|Sitemap