Polymer mixture with resistance against the influence of ethanol
a technology of polymer mixture and ethanol, which is applied in the direction of microcapsules, coatings, capsule delivery, etc., can solve the problems of toxic effects, assumed ideal ratios, and insufficient therapeutic effects, and achieve the effect of protecting against the influence of ethanol
- Summary
- Abstract
- Description
- Claims
- Application Information
AI Technical Summary
Benefits of technology
Problems solved by technology
Method used
Examples
embodiment
PREFERRED EMBODIMENT
[0088]In a preferred embodiment the polymer mixture may be a mixture from a
[0089]polymer 1, polymerized from a monomer mixture consisting of the monomers
[0090](a1) 70 to 95, preferably 85 to 95% by weight of 2-ethylhexyl methacrylate and 2-ethyl methacrylate at a ratio of from 3:1 to 1:1.
[0091](b1) 5 to 30, preferably 5-15% by weight of 2-trimethylammonium-ethyl-methacrylate-chloride and a polymer 2, polymerized from a monomer mixture consisting of the monomers
[0092](a2) 70 to 95, preferably 85 to 95% by weight of 2-ethylhexyl methacrylate and 2-ethyl methacrylate at a ratio from 3:1 to 1:1.
[0093](c2) 5-30, preferably 5-15% by weight of 2-hydroxyethyl methacrylate, wherein the polymer mixture is comprising polymer 1 to polymer 2 at a ratio by weight of from 2:1 to 1:2, and wherein polymer 1 to polymer 2 add up to 100%.
[0094]Preferably, the polymers 1 and / or 2 of the preferred embodiment may have one, two or three of the following properties in any possible combina
example 1
Polymerization
[0246]Table 1 summarizes the compositions of polymers 1 and 2 (according to the invention) and commercially available polymers EUDRAGIrRL, EUDRAGIT® RS and EUDRAGIT® NM (comparative, not according to the invention) with sustained release characteristics.
[0247]Abbreviations in table 1: (%=% by weight, Da=Dalton, Mw=weight-average molecular weight, Tmg=midpoint glass transition temperature, MFFT=minimum film forming temperature, D=Dispersity Index)
[0248]Procedure is described exemplarily for Polymer 1 (see Table 1). Polymer 2 was manufactured in the same manner. Setup consisted of a 1 L reaction vessel equipped with lid, agitator, condenser, nitrogen inlet and thermal sensor. Heating was carried out by a thermostat controlled water bath. A dosage pump with silicone tubes was used to dose monomer emulsion into the reaction mixture. In a first step, 534.0 g of water and 6.6 g of sodium dodecyl sulfate (SDS 15, 15.0% (w / w) aqueous solution) were dosed into the reactor, purge
example 2
f Polymer Dispersion on Metoprolol Succinate Pellets
[0251]Metoplolol Succinate pellets were obtained from Lee Pharma Limited (Telangana, India). Drug content is 40%. Particle size (determined by sieve analysis) is specified as follows: not more than 10% retains on sieve #16 ASTM and not more than 10% passes through sieve #25 ASTM (this relates to ca. 1 mm mean pellet diameter).
[0252]Dispersions of Polymer 1 and Polymer 2 (30% (w / w) polymer solid content) from Example 1 were used as is, or mixed in ratio 1:1.36 g talc (100% (w / w) compared to dry polymer mass) were suspended in 204 g water and homogenized using ultra turrax for 15 minutes. Subsequently, the prepared suspension was mixed with 120 g polymer dispersion (or dispersion mixture) and stirred for one hour. The amount of water for suspension of talc was calculated to result in a final spraying suspension of 20% (w / w) solid content. Coating experiments were carried out on a Huttlin (Schopfheim, Germany) Mycrolab (H00263), eq
PUM
Property | Measurement | Unit |
---|---|---|
Temperature | aaaaa | aaaaa |
Temperature | aaaaa | aaaaa |
Fraction | aaaaa | aaaaa |
Abstract
Description
Claims
Application Information
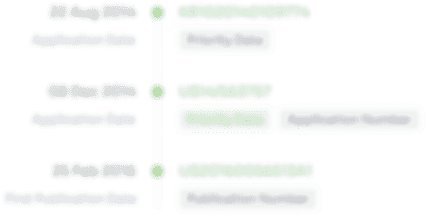
- R&D Engineer
- R&D Manager
- IP Professional
- Industry Leading Data Capabilities
- Powerful AI technology
- Patent DNA Extraction
Browse by: Latest US Patents, China's latest patents, Technical Efficacy Thesaurus, Application Domain, Technology Topic.
© 2024 PatSnap. All rights reserved.Legal|Privacy policy|Modern Slavery Act Transparency Statement|Sitemap