Method of manufacturing a liquid discharge head
- Summary
- Abstract
- Description
- Claims
- Application Information
AI Technical Summary
Problems solved by technology
Method used
Image
Examples
Example
SECOND EMBODIMENT
FIGS. 9A to 9J are views which illustrate a method for manufacturing the liquid discharge head represented in FIGS. 3A and 3B in accordance with a second embodiment of the present invention. The state of grooved film lamination is simplified.
At first, on the surface of the substrate 1 having the heat generating member 2 arranged thereon (FIG. 9A), the electrode layer 210 formed by TiW layer or nickel layer is arranged by means of sputtering method or the like (FIG. 9B).
Then, the electrode layer 210 is coated by resist 211. After that, the resist 211 is patterned corresponding to the configuration of the pedestal portion 7 (FIG. 9C).
Then, using gold 212 the electroformation is conducted on the surface of the substrate. Here, since the resist 211 has been patterned on the surface of the substrate corresponding to the configuration of the pedestal portion 7, only the portion where the resist 211 has been removed by patterning is electroformed (FIG. 9D).
After that, the res
Example
THIRD EMBODIMENT
FIGS. 10A to 10J are views which illustrate a method for manufacturing the liquid discharge head represented in FIGS. 3A and 3B in accordance with a third embodiment of the present invention. The state of the grooved film lamination is simplified.
At first, on the surface of the substrate 1 having the heat generating member 2 arranged thereon (FIG. 10A), the electrode layer 210 formed by TiW layer or nickel layer is arranged by means of sputtering method or the like (FIG. 10B).
Then, the electrode layer 210 is coated by resist 211. After that, the resist 211 is patterned corresponding to the configuration of the pedestal portion 7 (FIG. 10C).
Then, using gold 212 the electroformation is conducted on the surface of the substrate. Here, since the resist 211 has been patterned on the surface of the substrate corresponding to the configuration of the pedestal portion 7, only the portion where the resist 211 has been removed by patterning is electroformed (FIG. 10D).
After that,
Example
FOURTH EMBODIMENT
FIG. 11 is a cross-sectional view which shows a liquid discharge head manufactured by the method for manufacturing liquid discharge heads in accordance with another embodiment of the present invention, taken in the liquid flow path.
As shown in FIG. 11, the present embodiment comprises the heat generating member 2 that creates bubbles by the application of heat; the substrate 1 on which the heat generating members 2 are incorporated; the discharge ports 18 for discharging liquid; the orifice plate 19 having the discharge ports 18 formed therefor to determine the discharge direction of liquid; liquid flow paths 10 for supplying the discharge liquid to each of the discharge ports 18; the grooved member 51 that forms each of the liquid flow paths 10, the movable member 31 displaceable along the creation of bubbles on each of the heat generating members 2; and the pedestal portions 7 that support the movable members 31, respectively. Here, the groove walls 52 that separate
PUM
Property | Measurement | Unit |
---|---|---|
Flow rate | aaaaa | aaaaa |
Abstract
Description
Claims
Application Information
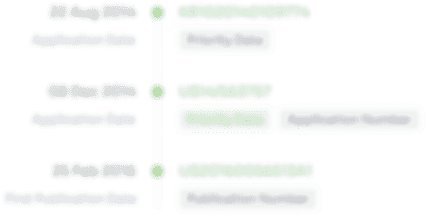
- R&D Engineer
- R&D Manager
- IP Professional
- Industry Leading Data Capabilities
- Powerful AI technology
- Patent DNA Extraction
Browse by: Latest US Patents, China's latest patents, Technical Efficacy Thesaurus, Application Domain, Technology Topic.
© 2024 PatSnap. All rights reserved.Legal|Privacy policy|Modern Slavery Act Transparency Statement|Sitemap