Polymers which exhibit thermothickening properties and process making same
- Summary
- Abstract
- Description
- Claims
- Application Information
AI Technical Summary
Benefits of technology
Problems solved by technology
Method used
Image
Examples
Example
EXAMPLE 1
Into a first vessel, an aqueous phase is prepared containing 243.7 parts of distilled water (a), 160.0 parts of 2-acrylamido-2-methylpropanesulfonic acid (b) (AMPS from Lubrizol), 40.0 parts of acrylic acid (c), 66.7 parts of Polyglycol B11 / 700 (d) (from Hoechst) and 12.0 parts of 50% NaOH (e). This phase is formed by dissolving AMPS and acrylic acid in water, mixing in NaOH solution and then adding Polyglycol B11 / 700.
Into a second vessel, an oil phase is prepared by mixing 12.0 parts of sorbitan monooleate (f), 10.0 parts of C12-C15 alcohols ethoxylated with 3 moles of ethylene oxide (g) and 6.0 parts of Hypermer B246 (h) (commercially available from ICI) in 170.0 parts of mineral spirits Shell Sol 151 (i) (commercially available from Shell). The aqueous phase is poured slowly into the oil phase while mixing, and the resulting mixture is homogenized in a blender for 15-25 seconds. The obtained monomer emulsion is then transferred to a reaction vessel equipped with an agit
Example
EXAMPLE 47
This example describe the characterization of thermothickening properties of the polymers thus made.
The thickening properties of the polymer are characterized by measuring the viscosity against salt concentration (salt thickening), temperature (thermal thickening) or shear rate (shear thickening). Polymer solution is either prepared with the above isolated solid product or with the inverted emulsion by nonyl phenol ethoxylated with 9 mols of ethylene oxide. The inversion of the emulsion is done by mixing 10.0 parts of the emulsion with 0.50 parts of nonyl phenol ethoxylated with 9 mol of ethylene oxide. The mixture is then diluted with 40.0 parts of water and neutralized with 1.14 parts of 50% (by weight) sodium hydroxide. This solution is then used for thickening characterization.
Sodium carbonate is used as the salt to show salt thickening. An 1.0% polymer solution is prepared either by diluting inverted emulsion or by dissolving the isolated solid in water. The viscosity is
Example
EXAMPLE 48
This example demonstrates that the non-ionic surfactants enhance the thermothickening of the polymer synthesized in Examples #1-45.
Polymer solution (0.5-1% by weight) is prepared by dissolving the isolated polymer in distilled water. To this solution is mixed in nonionic surfactant (0-2% by weight of Rhodasurf LA-7). If required, Ca(OH)2 is added to saturate the solution. The solution is heated and its viscosity at different temperature is recorded on a Brookfield LV viscometer at 60 rpm (shear rate 76.3 s−1). Polymers from Examples #1, #21, #32 (polymerized at 45, 55° C.), #34 (polymerized at 40° C.), #39 and #43 are tested with one or more of the nonionic surfactants, which are C12-15 alcohols ethoxylated with 3, 7 or 9 mols of ethylene oxide (an example of a representative surfactant having 7 mols of ethylene oxide is shown in FIG. 7).
TABLE 1Lubricant 50-HB-3520Polyglycol B11 / 700Example(MW 3520)(MW 5000)320.040.0430.030.0540.020.0660.0—
TABLE 2ExampleAmount of Components
PUM
Property | Measurement | Unit |
---|---|---|
Temperature | aaaaa | aaaaa |
Temperature | aaaaa | aaaaa |
Temperature | aaaaa | aaaaa |
Abstract
Description
Claims
Application Information
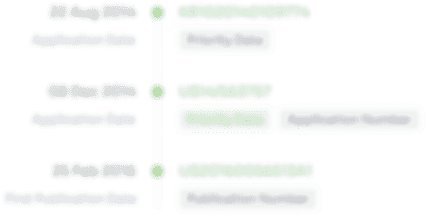
- R&D Engineer
- R&D Manager
- IP Professional
- Industry Leading Data Capabilities
- Powerful AI technology
- Patent DNA Extraction
Browse by: Latest US Patents, China's latest patents, Technical Efficacy Thesaurus, Application Domain, Technology Topic.
© 2024 PatSnap. All rights reserved.Legal|Privacy policy|Modern Slavery Act Transparency Statement|Sitemap