Self-adjusting hand tools utilizing a cam
- Summary
- Abstract
- Description
- Claims
- Application Information
AI Technical Summary
Benefits of technology
Problems solved by technology
Method used
Image
Examples
first embodiment
For the sake of this description, the first plier member assembly 12 shall be assumed to be in a fixed location. Thus the second plier member assembly 14 shall be described as moving relative to the first plier member assembly 12. FIGS. 2-5 show the operation of the pliers 10 that utilizes a release tab 160 extending from the second plier member assembly handle member 34 to actuate the cam assembly 130. In the first phase of operation, the jaw portions 16, 30 are initially separated and the cam assembly 130 has not engaged the tension member 66. The cam member 132 is maintained in a spaced relation from the tension member 66 by the second plier member assembly handle member release tab 160 contacting the cam assembly release pin 138. The second plier member assembly handle member 34 and the second plier member assembly second link 36 are held, relative to each other, at an initial toggle angle, indicated as α, by the toggle spring 150. With the second plier member assembly handle membe
second embodiment
As shown in FIGS. 13 and 14, the pliers 10A (second embodiment shown) are preferably constructed from a plurality of laminations 300, hereinafter, the laminate pliers 310. The laminations 300 are preferably cut or stamped from a sheet of metal. The laminations 300 form the various plier components, e.g., first plier member assembly 12 and second plier member assembly 14. The laminations 300 are erected in multiple layers. Preferably, the outer layers are mirror images of each other about a single center layer. That is, as shown in FIG. 13, the laminate pliers 310 have a first side 301 and a second side 302 and the components 12, 14 are made from mirror image laminations 300 on both the first and second sides 301, 302. For example, a laminate pliers 310 first plier member assembly 312 includes two generally flat members 311A, 311B forming a jaw portion 316, an intermediate portion 318 and a handle portion 320. The two first plier member assembly members 311A, 311B are the outermost laye
PUM
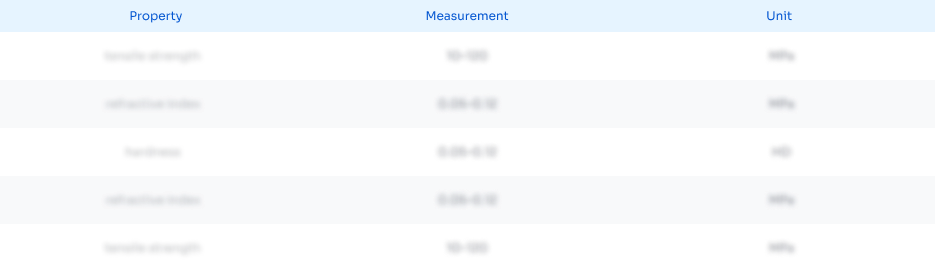
Abstract
Description
Claims
Application Information
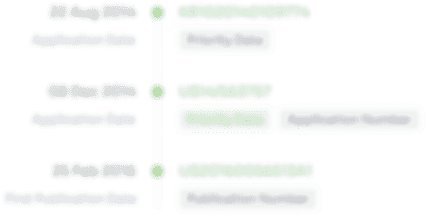
- R&D Engineer
- R&D Manager
- IP Professional
- Industry Leading Data Capabilities
- Powerful AI technology
- Patent DNA Extraction
Browse by: Latest US Patents, China's latest patents, Technical Efficacy Thesaurus, Application Domain, Technology Topic.
© 2024 PatSnap. All rights reserved.Legal|Privacy policy|Modern Slavery Act Transparency Statement|Sitemap