Lightweight forsterite brick and manufacturing method thereof
A technology of olivine brick and its manufacturing method, which is applied in the field of thermal insulation bricks for heat insulation of high-temperature kilns, can solve the problems of acid-base reaction and low applicable temperature range, reduce damage degree and speed, and improve thermal insulation effect and strength effect of satisfaction
- Summary
- Abstract
- Description
- Claims
- Application Information
AI Technical Summary
Benefits of technology
Problems solved by technology
Method used
Image
Examples
Embodiment 1
[0024] First olivine sand (MgO 43%, SiO 2 38%) and magnesia (MgO 87%) are mechanically crushed by a crusher respectively, and sieved by a 1.5mm sieve to make granular materials with a particle size of ≤1.5mm, and a part thereof is processed into 200-mesh fine powder with a ball mill; Coke and charcoal are also made into pellets of ≤1.5mm;
[0025] According to the weight in Table 1, weigh the granules of olivine sand, magnesia, coke and charcoal, put them into the sand mixer, and dry mix them for 3 to 5 minutes to make them evenly mixed; Mix for 3 to 5 minutes, add olivine and magnesia fine powder, and mix for another 8 to 10 minutes; inject the mixed material into the mold, pressurize it on a 200t friction brick press to obtain a wet billet; put the wet billet at 25 to Naturally dry at 35°C for 25 hours, send it into the drying kiln, control the hot air inlet temperature of the drying kiln at 100-120°C, and the outlet temperature at 40-60°C, and dry for 17 hours; 1390°C±5°C hi
Embodiment 2
[0027] First olivine sand (MgO 44%, SiO 2 39%) and magnesia (MgO 90%) are mechanically crushed by a crusher respectively, and sieved by a 1.5mm sieve to make granular materials with a particle size of ≤1.5mm, and a part thereof is processed into 200-mesh fine powder with a ball mill; Coke and charcoal are also made into pellets of ≤1.5mm;
[0028] According to the weight in Table 1, weigh the granules of olivine sand, magnesia, coke and charcoal, put them into the sand mixer, and dry mix them for 3 to 5 minutes to make them evenly mixed; Mix for 3 to 5 minutes, add olivine and magnesia fine powder, and mix for another 8 to 10 minutes; inject the mixed material into the mold, pressurize it on a 200t friction brick press to obtain a wet billet; put the wet billet at 25 to Naturally dry at 35°C for 28 hours, send it into the drying kiln, control the hot air inlet temperature of the drying kiln at 100-120°C, and the outlet temperature at 40-60°C, and dry for 18 hours; 1350°C high-t
Embodiment 3
[0030] First olivine sand (MgO 45%, SiO 2 40%) and magnesia (MgO 92%) are mechanically crushed by a crusher respectively, and sieved by a 1.5mm sieve to make granular materials with a particle size of ≤1.5mm, and a part thereof is processed into 200-mesh fine powder with a ball mill; Coke and charcoal are also made into pellets of ≤1.5mm;
[0031] According to the weight in Table 1, weigh the granules of olivine sand, magnesia, coke and charcoal, put them into the sand mixer, and dry mix them for 3 to 5 minutes to make them evenly mixed; Mix for 3 to 5 minutes, add olivine and magnesia fine powder, and mix for another 8 to 10 minutes; inject the mixed material into the mold, pressurize it on a 100t friction brick press, and obtain a wet billet; mix the wet billet for 25 to 35 Naturally dry at ℃ for 24 hours, send it into the drying kiln, control the hot air inlet temperature of the drying kiln at 100-120 ℃, and the outlet temperature at 40-60 ℃, and dry for 16 hours; ℃ high-tem
PUM
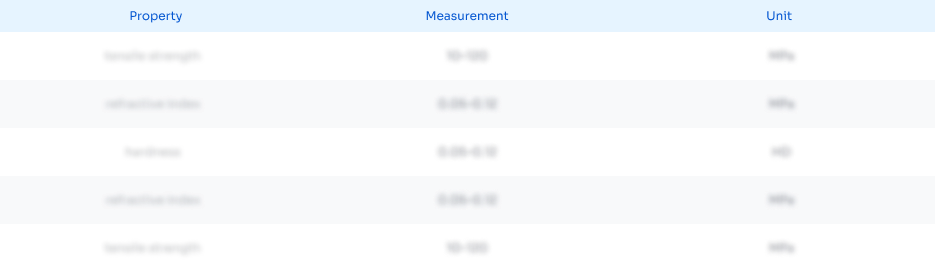
Abstract
Description
Claims
Application Information
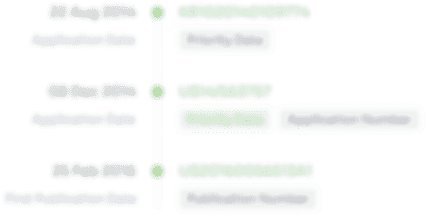
- R&D Engineer
- R&D Manager
- IP Professional
- Industry Leading Data Capabilities
- Powerful AI technology
- Patent DNA Extraction
Browse by: Latest US Patents, China's latest patents, Technical Efficacy Thesaurus, Application Domain, Technology Topic.
© 2024 PatSnap. All rights reserved.Legal|Privacy policy|Modern Slavery Act Transparency Statement|Sitemap