Method for preparing catalyst with non-uniform distribution of active metal component
A non-uniform distribution and active metal technology, applied in the direction of catalyst activation/preparation, metal/metal oxide/metal hydroxide catalyst, chemical instruments and methods, etc., can solve the problems of long production process and achieve simplification of preparation methods, The effect of high hydrodemetallization activity and good metal performance
- Summary
- Abstract
- Description
- Claims
- Application Information
AI Technical Summary
Problems solved by technology
Method used
Image
Examples
Embodiment 1
[0025] Take by weighing 1000g of aluminum hydroxide powder (dried rubber powder produced by the Catalyst Factory of Changling Refining and Chemical Company), extrude it into a cylindrical strip with a circumscribed circle diameter of 1.2 mm with an extruder, dry the wet strip at 120°C for 4 hours, and then dry it at 900°C Calcined for 4 hours, the obtained alumina carrier is marked as Z1. Its water absorption was measured to be 1.04 ml / g.
[0026] Weigh 200g of carrier Z1, and add the above substances into deionized water in the order of tartaric acid, ammonium paramolybdate, and nickel nitrate in turn. The ratio of the moles of tartaric acid to the sum of the moles of ammonium paramolybdate and nickel nitrate is 0.2, of which nickel nitrate (containing NiO25%) is 8.83g, ammonium molybdate (containing MoO 3 82%) was 20.2 g, and 209 ml of deionized water was added, stirred evenly until completely dissolved, and an impregnating solution was obtained. After mixing evenly, use a
Embodiment 2
[0028]Take by weighing 1000g of aluminum hydroxide powder (dry rubber powder produced by Changling Refining and Chemical Company Catalyst Factory), use an extruder to form a cylindrical strip with a circumscribed circle diameter of 1.2 mm, dry the wet strip at 120°C for 4 hours, and then dry it at 800°C Calcined for 4 hours, the obtained alumina carrier is marked as Z2.
[0029] Weigh 200g and the water absorption rate is 1.04ml.g -1 Carrier Z2, add the above substances into deionized water in the order of citric acid, TW-20, ammonium paramolybdate, and cobalt nitrate, wherein cobalt nitrate (containing CoO25.8%) is 10.19g, ammonium molybdate (containing MoO 3 82%) was 22.4 g. The ratio of the moles of citric acid to the sum of the moles of ammonium paramolybdate and cobalt nitrate is 0.65, and the molar ratio of the surfactant TW-20 added at the same time to the amount of citric acid is 0.4. Add 210ml of deionized water, stir well until completely dissolved. After mixing even
Embodiment 3
[0031] Weigh 1000g of aluminum hydroxide powder (same as Example 1), use an extruder to form a cylindrical strip with a circumscribed circle diameter of 1.2 mm, dry the wet strip at 120°C for 4 hours, and roast at 600°C for 4 hours to obtain alumina The carrier is denoted Z3.
[0032] Weigh 200g and the water absorption rate is 0.96ml.g -1 γ-Al 2 o 3 Carrier, add the above substances into deionized water in the order of phosphoric acid, TW-80, ammonium metatungstate, and nickel nitrate, in which nickel nitrate (containing NiO25%) is 7.23g, and the added ammonium metatungstate is For the ammonium 8.5m% solution, the ratio of the moles of phosphoric acid to the sum of the moles of ammonium metatungstate and nickel nitrate is 0.8, and the molar ratio of TW-80 of the surfactant added to phosphoric acid is 0.65. Add 204ml of deionized water until completely dissolved, mix evenly, and measure the pH value of the soaking solution with a pH meter to be 3.12. The carrier was immersed
PUM
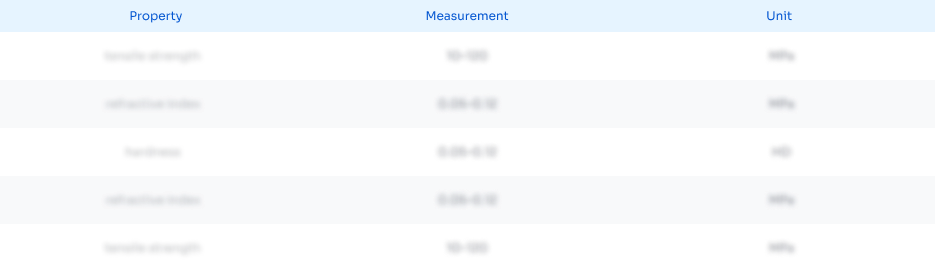
Abstract
Description
Claims
Application Information
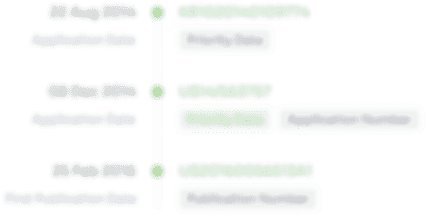
- R&D Engineer
- R&D Manager
- IP Professional
- Industry Leading Data Capabilities
- Powerful AI technology
- Patent DNA Extraction
Browse by: Latest US Patents, China's latest patents, Technical Efficacy Thesaurus, Application Domain, Technology Topic.
© 2024 PatSnap. All rights reserved.Legal|Privacy policy|Modern Slavery Act Transparency Statement|Sitemap