Method for measuring groove position of inner bearing ring
A technology of bearing inner sleeve and measurement method, applied in the direction of mechanical clearance measurement, etc., can solve the problems of increasing the production cost of the enterprise, the error of the actual groove position value and the actual assembly groove position value, and the different measurement methods, so as to reduce the production cost and improve the The effect of measurement accuracy and simple measurement method
- Summary
- Abstract
- Description
- Claims
- Application Information
AI Technical Summary
Benefits of technology
Problems solved by technology
Method used
Image
Examples
Embodiment Construction
[0017] The present invention will be described in further detail below in conjunction with the accompanying drawings and embodiments.
[0018] See attached picture. The present embodiment includes a base 1 as a measuring plane, on which a column 2 is vertically fixed, on the column 2 there is a connecting rod 3 parallel to the base, on which a thousand points Instrument 4; the measuring end of the micrometer 4 is a measuring ball 5, and the diameter d of the measuring ball 5 is the same as the channel radius R of the bearing inner sleeve 6 under test.
[0019] Using the above-mentioned measuring device, when measuring in this embodiment, the height H of the end surface of the inner sleeve 6 of the bearing under test is firstly measured by the pad gauge method. 实 and the height C of the assembly surface of the bearing inner sleeve 6 under test 实 ; Then according to the theoretical value A of the bearing inner sleeve groove position 0 and the end face height H of the bearing in
PUM
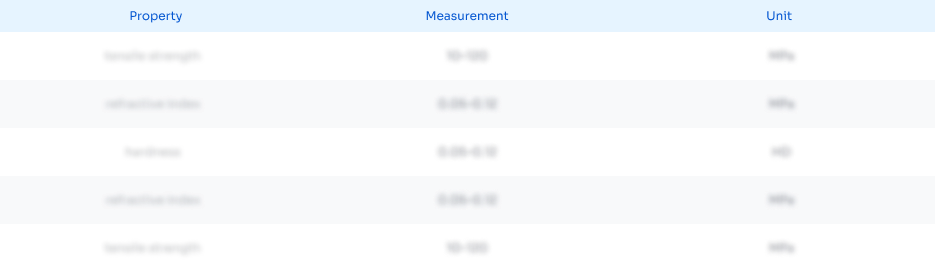
Abstract
Description
Claims
Application Information
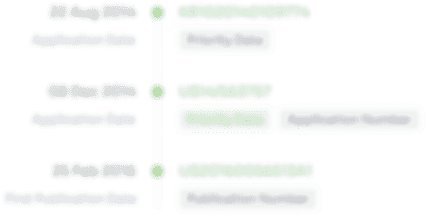
- R&D Engineer
- R&D Manager
- IP Professional
- Industry Leading Data Capabilities
- Powerful AI technology
- Patent DNA Extraction
Browse by: Latest US Patents, China's latest patents, Technical Efficacy Thesaurus, Application Domain, Technology Topic.
© 2024 PatSnap. All rights reserved.Legal|Privacy policy|Modern Slavery Act Transparency Statement|Sitemap