Low acetated cellulose fibers and preparation method thereof
A technology of cellulose acetate and cellulose, which is applied in the field of low-acetate cellulose fiber and its preparation, can solve the problems of inability to achieve uniform dispersion of acetic anhydride, poor anti-fibrillation performance of cellulose fiber, high consumption pollution, etc. problems, to achieve uniform microcosmic condensate structure, long-lasting anti-fibrillation performance, and low fibrillation index
- Summary
- Abstract
- Description
- Claims
- Application Information
AI Technical Summary
Benefits of technology
Problems solved by technology
Method used
Image
Examples
Embodiment 1
[0046] At room temperature, mix 19 parts of acetic anhydride into 1250 parts of acetic acid 1-ethyl-3-methylimidazole, mix evenly, then mix 100 parts of cellulose into the solvent, stir and mix, at a pressure of 1.0×10 3 Pa~1.0×10 5 Under the condition of Pa, the temperature is raised to 60°C, and it reacts while dissolving to obtain a uniform, transparent and stable spinning stock solution. The average degree of substitution of cellulose in the stock solution is 0.261, and the viscosity of the stock solution is 350,000 mPaS. The silk is stretched 1.4 times in the first bath, 1.2 times in the second bath, and 1.2 times in the third bath. The coagulation bath and the drawing bath are aqueous solutions of EMIMAc, with concentrations of 80%, 25%, and 10%, and finally washed, drying to obtain the low acetate cellulose fiber. The fiber breaking strength is 3.6cN / dtex, the breaking elongation is 19%, the fineness is 2.26dtex, the fiber fibrillation index is below 2, the fiber feels
Embodiment 2
[0048] At room temperature, mix 8 parts of ethanol and 30 parts of acetic anhydride into 800 parts of acetic acid 1-ethyl-3-methylimidazole, mix well, then mix 120 parts of cellulose into the solvent, stir and mix, and the pressure is 1.0×10 3 Pa~1.0×10 5 Under the condition of Pa, the temperature is raised to 75°C, and it reacts while dissolving to obtain a uniform, transparent and stable spinning stock solution. The average degree of substitution of cellulose in the stock solution is 0.305, and the viscosity of the stock solution is 1.35 million mPaS. , the nozzle is stretched 6 times, and the silk is drawn 1 time in the first bath, 1.5 times in the second bath, and 1.4 times in the third bath. The coagulation bath and the drawing bath are aqueous solutions of EMIMAc, and the concentrations are 60% and 25% in turn. , 10%, which also contains part of the ethanol extracted from the stock solution, the total draft ratio of the silk is 12.6 times, and finally washed and dried to ob
Embodiment 3
[0050] At room temperature, mix 25 parts of acetic anhydride into 913 parts of 1-butyl-3-methylimidazole acetate, mix evenly, then mix 200 parts of cellulose into the solvent, stir and mix, and the pressure is 1.0×10 3 Pa~1.0×10 5 Under the condition of Pa, the temperature is gradually raised to 95°C, and reacts while dissolving to obtain a uniform, transparent and stable spinning stock solution. The average degree of substitution of cellulose in the stock solution is 0.112, and the viscosity of the stock solution is 1.4 million mPaS. Silk, the nozzle is drawn 8 times, and the silk is drawn 1.4 times in the first bath, 0.7 times in the second bath, and 1.3 times in the third bath. The coagulation bath and the drawing bath are aqueous solutions of BMIMAc, and the concentrations are 80%, 25 %, 10%, the total drafting ratio of the silk is 10.2 times, and finally washed and dried to obtain the low-acetate cellulose fiber. The fiber breaking strength is 4.6cN / dtex, the breaking elo
PUM
Property | Measurement | Unit |
---|---|---|
Viscosity | aaaaa | aaaaa |
Breaking strength | aaaaa | aaaaa |
Fineness | aaaaa | aaaaa |
Abstract
Description
Claims
Application Information
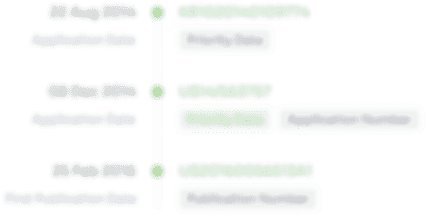
- R&D Engineer
- R&D Manager
- IP Professional
- Industry Leading Data Capabilities
- Powerful AI technology
- Patent DNA Extraction
Browse by: Latest US Patents, China's latest patents, Technical Efficacy Thesaurus, Application Domain, Technology Topic.
© 2024 PatSnap. All rights reserved.Legal|Privacy policy|Modern Slavery Act Transparency Statement|Sitemap