Method for preparing zinc oxide nanowire film
A technology for zinc oxide nanowires and films, applied in the field of preparing zinc oxide nanowire films, can solve the problems of difficult operation, complicated process and high cost, and achieve the effects of unlimited area, large film area and simple method.
- Summary
- Abstract
- Description
- Claims
- Application Information
AI Technical Summary
Benefits of technology
Problems solved by technology
Method used
Image
Examples
preparation example Construction
[0045] 4), preparation of suspension
[0046] The surface-modified zinc oxide nanowires are placed in deionized water and ultrasonically dispersed to obtain a uniform suspension; the mass-volume ratio of the surface-modified zinc oxide nanowires to deionized water is 0.2-0.5 mg / mL. The time of ultrasonic treatment is 1~3h, and the power density is 60~100W / m 2 , The frequency of ultrasonic waves is 40-80kHz.
[0047] 5) Self-assembly of ZnO nanowires
[0048] The silicon wafer with the silicon dioxide layer that has undergone hydrophilic treatment is placed in a uniform suspension solution and left to stand to obtain a zinc oxide nanowire film. The time used for standing still is 2~24h.
Embodiment 1
[0052] Put a silicon wafer with a silicon dioxide layer with a specification of 3 into 50 ml of acetone, at an ultrasonic frequency of 60KHz and a power density of 80W / m 2 Under the conditions of ultrasonic cleaning for 10 minutes, take it out and dry it with nitrogen; then, put the silicon wafer with the silicon dioxide layer into 50 ml of ethanol, at the ultrasonic frequency of 60KHz, the ultrasonic power density of 80W / m 2 Under the condition of ultrasonic cleaning for 10 minutes, take it out and dry it with nitrogen gas; finally put the silicon wafer with silicon dioxide layer into 100 ml of deionized water, at the ultrasonic frequency of 60KHz and the ultrasonic power density of 80W / m 2 Ultrasonic cleaning was performed for 10 minutes under certain conditions, and then it was taken out and blown dry with nitrogen gas.
[0053] With a concentration of 30wt% sulfuric acid solution and 98wt% hydrogen peroxide solution, the volume ratio of the sulfuric acid solution to the
Embodiment 2
[0059] Put a silicon wafer with a silicon dioxide layer with a specification of 3 into 50 ml of acetone, when the frequency of the ultrasonic wave is 60KHz, and the power density of the ultrasonic wave is 80W / m 2 Under the conditions of ultrasonic cleaning for 10 minutes, take it out and dry it with nitrogen; then, put the silicon wafer with the silicon dioxide layer into 50 ml of ethanol, at the ultrasonic frequency of 60KHz, the ultrasonic power density of 80W / m 2 Under the condition of ultrasonic cleaning for 10 minutes, take it out and dry it with nitrogen gas; finally put the silicon wafer with silicon dioxide layer into 100 ml of deionized water, at the ultrasonic frequency of 60KHz and the ultrasonic power density of 80W / m 2 Ultrasonic cleaning was performed for 10 minutes under certain conditions, and then it was taken out and blown dry with nitrogen gas.
[0060] Be that the sulfuric acid solution with concentration 30wt% and concentration be the hydrogen peroxide
PUM
Property | Measurement | Unit |
---|---|---|
Power density | aaaaa | aaaaa |
Abstract
Description
Claims
Application Information
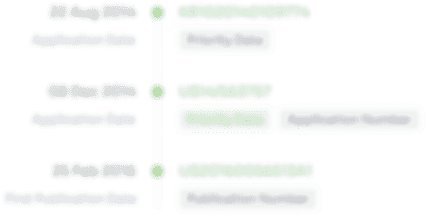
- R&D Engineer
- R&D Manager
- IP Professional
- Industry Leading Data Capabilities
- Powerful AI technology
- Patent DNA Extraction
Browse by: Latest US Patents, China's latest patents, Technical Efficacy Thesaurus, Application Domain, Technology Topic.
© 2024 PatSnap. All rights reserved.Legal|Privacy policy|Modern Slavery Act Transparency Statement|Sitemap