High-performance anti-corrosion composite coating material and preparation method thereof
A composite coating and high-performance technology, applied in the direction of anti-corrosion coatings, coatings, etc., can solve the problems of high requirements and difficult control of spraying process, and achieve the effect of improving compressive strength, good construction effect and convenient temperature conditions
- Summary
- Abstract
- Description
- Claims
- Application Information
AI Technical Summary
Problems solved by technology
Method used
Image
Examples
Embodiment 1
[0032] (1) Weigh 30 parts of fluororesin monomer, 30 parts of styrene monomer and 40 parts of hexamethylcyclotrisiloxane monomer and mix evenly, add to 4 parts of polyethylene glycol octylphenyl ether, 4 parts Parts of polyethylene glycol, 3 parts of polyethylene glycol stearate and 100 parts of water, then weigh 5 parts of sericite powder, 2 parts of azobisisobutyronitrile, and 1 part of lauryl phenylacetate After mixing evenly, add it to the above solution, keep the water bath at constant temperature and wet grind until the mixture is uniform, and obtain the modified fluororesin emulsion. The ball is a steel ball, and the diameter of the wet grinding ball is 1mm.
[0033](2) Weigh 100 parts of fly ash and 20 parts of water glass and mix and stir for 1 minute, then slowly add 45 parts of water and 0.2 parts of polycarboxylate water reducer and mix and stir for 2 minutes until evenly mixed to obtain water glass activated fly ash .
[0034] (3) Take by weighing 50 parts of mo...
Embodiment 2
[0036] (1) Weigh 35 parts of fluororesin monomer, 35 parts of styrene monomer and 25 parts of hexamethylcyclotrisiloxane monomer and mix them uniformly, add to 5 parts of polyethylene glycol octylphenyl ether, 5 parts Parts of polyethylene glycol, 5 parts of polyethylene glycol stearate and 120 parts of water, then weigh 6 parts of sericite powder, 3 parts of azobisisoheptanonitrile, 2 parts of phenylethyl alcohol oleate After mixing evenly, add it to the above solution, keep the water bath at constant temperature and wet mill until evenly mixed to obtain a modified fluororesin emulsion. The ball is a ceramic ball, and the diameter of the wet grinding ball is 1mm.
[0037] (2) Weigh 150 parts of fly ash and 25 parts of water glass, mix and stir for 1 min, then slowly add 30 parts of water and 0.3 parts of HSB fat water reducer and mix and stir for 3 min until the mixture is evenly mixed to obtain water glass activated fly ash.
[0038] (3) Take by weighing 60 parts of modifie...
Embodiment 3
[0040] (1) Weigh 30 parts of fluororesin monomer, 45 parts of styrene monomer and 30 parts of hexamethylcyclotrisiloxane monomer and mix evenly, add to 6 parts of polyethylene glycol octylphenyl ether, 6 parts Parts of polyethylene glycol, 7 parts of polyethylene glycol stearate and 150 parts of water, then weigh 7 parts of sericite powder, 3 parts of azobisisobutyronitrile, and 2 parts of phenylethyl alcohol oleate After mixing evenly, add it to the above solution, and wet-mill it in a water bath until it is evenly mixed to obtain a modified fluororesin emulsion. The ball is an agate ball, and the diameter of the wet grinding ball is 2mm.
[0041] (2) Weigh 140 parts of fly ash and 30 parts of water glass and mix and stir for 1 minute, then slowly add 35 parts of water and 0.3 part of polycarboxylate water reducer and mix and stir for 4 minutes until the mixture is uniform to obtain water glass activated fly ash .
[0042] (3) Take by weighing 100 parts of the modified fluo...
PUM
Property | Measurement | Unit |
---|---|---|
Diameter | aaaaa | aaaaa |
Abstract
Description
Claims
Application Information
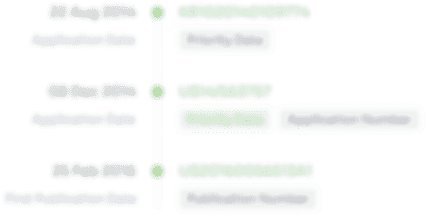
- R&D Engineer
- R&D Manager
- IP Professional
- Industry Leading Data Capabilities
- Powerful AI technology
- Patent DNA Extraction
Browse by: Latest US Patents, China's latest patents, Technical Efficacy Thesaurus, Application Domain, Technology Topic.
© 2024 PatSnap. All rights reserved.Legal|Privacy policy|Modern Slavery Act Transparency Statement|Sitemap