Bi Cu 1-x SeO-based oxide thermoelectric ceramic material and preparation method thereof
A ceramic material and oxide technology, applied in the field of BiCu1-xSeO-based oxide thermoelectric ceramic materials and their preparation, can solve the problems of complex sintering process, cumbersome process cost, etc., and achieve low sintering temperature, short reaction time, and improved sample performance. Effect
- Summary
- Abstract
- Description
- Claims
- Application Information
AI Technical Summary
Problems solved by technology
Method used
Image
Examples
Embodiment 1
[0027] Example 1. Preparation of BiCuSeO-based oxide thermoelectric ceramic material
[0028] According to the stoichiometric ratio in BiCuSeO, weigh Bi, Cu, Se and Bi 2 o 3 , after mixing, the mixed material is obtained; the mixed material is placed in a ball mill tank for dry grinding, the rotation speed is 400rpm, and the time is 8h to obtain the precursor powder; the precursor powder is dried at 60°C for 12h; then the powder is put into Spark plasma sintering is carried out in a graphite abrasive tool, the heating rate is controlled to be 300°C / min, the final temperature is 300°C for 6 minutes, and the pressure is 50Mpa; then the heating rate is controlled to be 300°C / min, and the final temperature is 700°C for 8 minutes by discharge plasma sintering , the pressure is 50Mpa, and the BiCuSeO-based oxide thermoelectric ceramic material is obtained.
[0029] The XRD spectrum pattern of the sample prepared by this embodiment is as figure 1 As shown, it can be seen from the
Embodiment 2
[0031] Embodiment 2, preparation BiCu 0.985 SeO-based oxide thermoelectric ceramic materials
[0032] According to BiCu 0.985 Stoichiometric ratio in SeO, weighing Bi, Cu, Se and Bi 2 o 3 , after mixing, the mixed material is obtained; the mixed material is placed in a ball mill tank for dry grinding, the rotation speed is 250rpm, and the time is 2h, to obtain the precursor powder; the precursor powder is dried at 50°C for 24h; then the powder is put into Spark plasma sintering was carried out in a graphite abrasive tool, the heating rate was controlled to be 50°C / min, the final temperature was 200°C for 4 minutes, and the pressure was 30Mpa; then the heating rate was controlled to be 50°C / min, and the final temperature was 600°C for 4 minutes by discharge plasma sintering , the pressure is 30Mpa, to get BiCu 0.985 SeO-based oxide thermoelectric ceramic materials.
[0033] The XRD spectrum pattern of the sample prepared by this embodiment is as figure 1 As shown, it can
Embodiment 3
[0035]Embodiment 3, preparation BiCu 0.975 SeO-based oxide thermoelectric ceramic materials
[0036] According to BiCu 0.975 Stoichiometric ratio in SeO, weighing Bi, Cu, Se and Bi 2 o 3 , after mixing, the mixed material is obtained; the mixed material is placed in a ball mill tank for dry grinding, the rotation speed is 300rpm, and the time is 10h to obtain the precursor powder; the precursor powder is dried at 70°C for 4h; then the powder is put into Spark plasma sintering is carried out in graphite abrasive tools, control the heating rate to 150°C / min, sinter at a final temperature of 250°C for 10 minutes, and a pressure of 40Mpa; then control the heating rate to 150°C / min, and discharge plasma sintering at a final temperature of 650°C for 10 minutes , the pressure is 40Mpa, to get BiCu 0.975 SeO-based oxide thermoelectric ceramic materials.
[0037] The XRD spectrum pattern of the sample prepared by this embodiment is as figure 1 As shown, it can be seen from the f
PUM
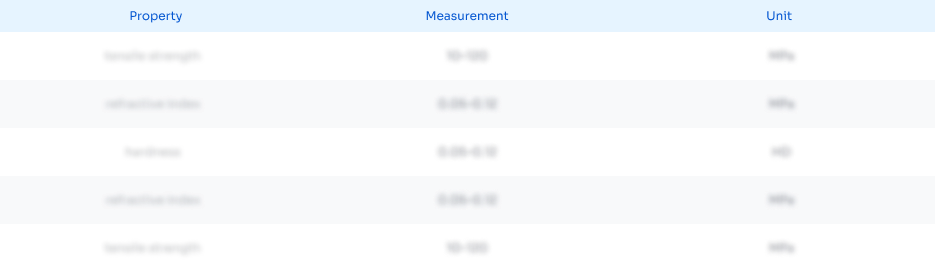
Abstract
Description
Claims
Application Information
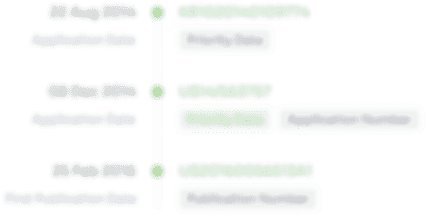
- R&D Engineer
- R&D Manager
- IP Professional
- Industry Leading Data Capabilities
- Powerful AI technology
- Patent DNA Extraction
Browse by: Latest US Patents, China's latest patents, Technical Efficacy Thesaurus, Application Domain, Technology Topic.
© 2024 PatSnap. All rights reserved.Legal|Privacy policy|Modern Slavery Act Transparency Statement|Sitemap