Proportioning method for recycling waste residues of valuable metal through sulphur fixation treatment
A valuable metal and sulfur treatment technology, applied in the field of proportioning, can solve the problems of reducing product output, environmental pollution, consumption of mineral resources, etc., to save electricity costs and equipment maintenance costs, high purity and extraction rate, huge The effect of economic benefits
- Summary
- Abstract
- Description
- Claims
- Application Information
AI Technical Summary
Benefits of technology
Problems solved by technology
Method used
Examples
Embodiment Construction
[0014] The technical scheme of the present invention will be further described below through specific embodiments:
[0015] The present invention provides a method for mixing waste slag of valuable metals by using sulfur fixation treatment. The steps include material preparation, compaction, sulfur fixation treatment and purification. mixed, and the ratio of the lead-containing waste residue, iron material and fuel is 60-80:15-35:3-5.
[0016] Wherein, the lead grade in the lead-containing waste residue is greater than 20%; the iron content in the iron material is greater than 50%; the fixed carbon in the fuel is greater than 70%.
[0017] The briquetting step is intended to briquette the mixture with a coal press;
[0018] In the sulfur-fixing smelting step, the purpose is to put the compressed coal agglomerates and coke into the side-blown smelting furnace to carry out the sulfur-fixing reduction reaction;
[0019] After the sulfur-fixing smelting step, lead alloy, iron sulfi
PUM
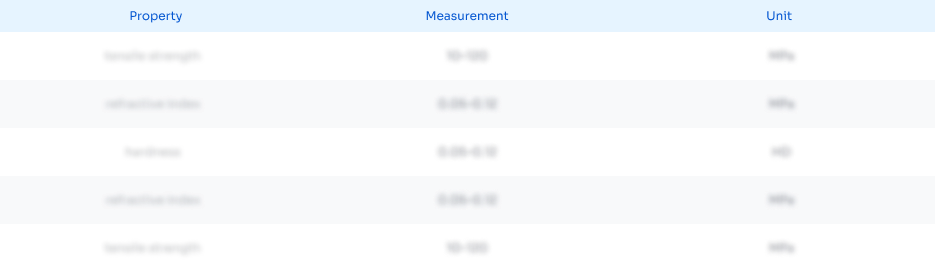
Abstract
Description
Claims
Application Information
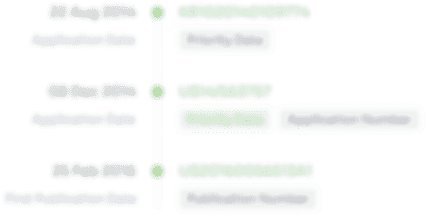
- R&D Engineer
- R&D Manager
- IP Professional
- Industry Leading Data Capabilities
- Powerful AI technology
- Patent DNA Extraction
Browse by: Latest US Patents, China's latest patents, Technical Efficacy Thesaurus, Application Domain, Technology Topic.
© 2024 PatSnap. All rights reserved.Legal|Privacy policy|Modern Slavery Act Transparency Statement|Sitemap