Composite shaping technique method of iron pattern coated sand and iron type core assembly
A technology of composite modeling and process method, applied in the directions of molding machines, manufacturing tools, casting and molding equipment, etc., can solve the problem of high hardness of parts, and achieve the effect of maintaining uniform hardness
- Summary
- Abstract
- Description
- Claims
- Application Information
AI Technical Summary
Benefits of technology
Problems solved by technology
Method used
Examples
Embodiment 1
[0015] The iron mold sand-covered and iron mold core composite molding process for casting ductile iron parts includes the following steps: A. Make the upper mold of the part casting mold: set the iron mold of the part heated to 210 °C outside the electric heating pattern of the part, and the electric heating pattern of the part Heat to 210°C; use a sand-coating machine to inject the coated sand between the iron mold of the part and the electric heating pattern of the part. The sand-injecting pressure of the sand-coating machine is 0.35MPa, the sand-injecting time is 3 seconds, and the heating and curing temperature is 210°C. The heating and curing time is 12 seconds, and the coated sand is solidified into a sand shell with a thickness of 6 mm to 8 mm and adhered to the inner wall of the iron mold of the part; the mold is lifted, the electric heating pattern of the part is taken out, and trimmed to obtain the upper mold of the part; B 1. Make the coated sand core of the part: inst
Embodiment 2
[0018] The iron mold sand-covered and iron mold core composite molding process for casting ductile iron parts includes the following steps: A. Make the upper mold of the part casting mold: set the iron mold of the part heated to 240 °C outside the electric heating pattern of the part, and the electric heating pattern of the part Heat to 240°C; use a sand-coating machine to inject the coated sand between the iron mold of the part and the electric heating pattern of the part. The sand-injecting pressure of the sand-coating machine is 0.35MPa, the sand-injecting time is 6 seconds, and the heating and curing temperature is 240°C. The heating and curing time is 15 seconds, and the coated sand is solidified into a 6 mm to 8 mm thick sand shell that sticks to the inner wall of the iron mold of the part; B. Make the coated sand core of the part: install the electric heating core box of the part on the core shooting machine, and close the mold; heat the electric heating core box of the par
PUM
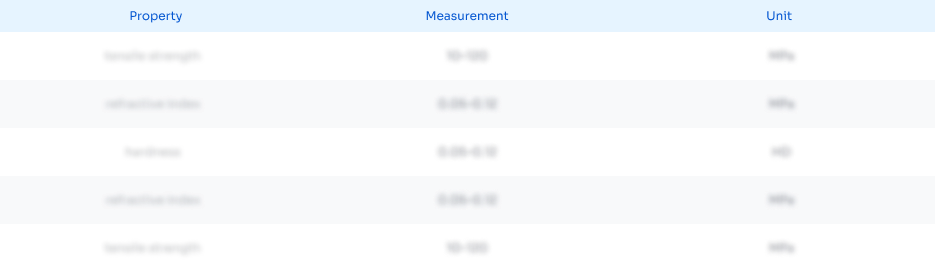
Abstract
Description
Claims
Application Information
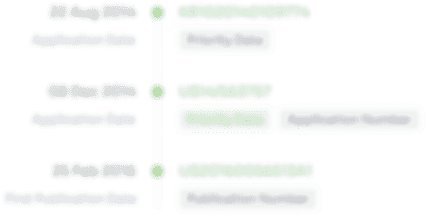
- R&D Engineer
- R&D Manager
- IP Professional
- Industry Leading Data Capabilities
- Powerful AI technology
- Patent DNA Extraction
Browse by: Latest US Patents, China's latest patents, Technical Efficacy Thesaurus, Application Domain, Technology Topic.
© 2024 PatSnap. All rights reserved.Legal|Privacy policy|Modern Slavery Act Transparency Statement|Sitemap