Biaxial stretching polypropylene high heat-seal film and manufacturing method thereof
A biaxially stretched, polypropylene technology, applied in the polymer field, can solve the problems of unfavorable packaging, reduced film strength, broken packages, etc., and achieve the effect of good physical and mechanical properties
- Summary
- Abstract
- Description
- Claims
- Application Information
AI Technical Summary
Problems solved by technology
Method used
Image
Examples
Embodiment 1
[0026] Films with a thickness of 23 μm were produced. Ingredients: The thickness of the upper layer is 4 μm, and the raw materials include 88% polypropylene copolymer, 10% ethylene-acrylate copolymer and 2% synthetic silica; the thickness of the middle layer is 15 μm, and the raw materials include 88% homopolypropylene, 10% ethylene-acrylate Copolymer and 2% ethoxylated amine; the lower layer is 4 µm thick and consists of 88% copolymerized polypropylene, 10% ethylene-acrylate copolymer and 2% synthetic silica.
[0027] Film production: The biaxially oriented polypropylene high heat-sealing strength film of the present invention is produced by using a biaxially oriented co-extrusion process, wherein the temperature of the extruder: 235°C; the temperature of the casting machine: 25°C; the longitudinal stretch ratio: 493%; Longitudinal stretching preheating temperature: 112°C; longitudinal stretching temperature: 100°C; transverse stretching ratio: 920%; transverse stretching prehea
Embodiment 2
[0029] Films with a thickness of 30 μm were produced. Ingredients: the upper layer is 5 μm thick, and the raw materials include 90% polypropylene copolymer, 8% ethylene-acrylate copolymer and 2% synthetic silica; the middle layer is 15 μm thick, and the raw materials include 90% homopolypropylene, 8% ethylene-acrylate Copolymer and 2% ethoxylated amine. The lower layer is 5 μm thick, and the raw materials include 90% copolymerized polypropylene, 8% ethylene-acrylate copolymer and 2% synthetic silica.
[0030] Film production: The biaxially oriented polypropylene high heat-sealing strength film of the present invention is produced by using a biaxially oriented co-extrusion process, wherein the temperature of the extruder: 220°C; the temperature of the casting machine: 20°C; the longitudinal stretch ratio: 490%; Preheating temperature for longitudinal stretching: 120°C; stretching temperature for longitudinal stretching: 100°C; transverse stretching ratio: 850%; preheating tempera
Embodiment 3
[0032] Films with a thickness of 20 μm were produced. Ingredients: the upper layer is 3 μm thick, of which 85% copolymerized polypropylene, 13% ethylene-acrylate copolymer and 2% synthetic silica; the middle layer is 14 μm thick, of which 88% homopolypropylene, 10% ethylene-acrylate copolymer and 2% % ethoxylated amines. The lower layer is 3 μm thick and consists of 85% copolymerized polypropylene, 13% ethylene-acrylate copolymer and 2% synthetic silica.
[0033] Film production: The biaxially oriented polypropylene high heat-sealing strength film of the present invention is produced by using a biaxially oriented co-extrusion process, wherein the temperature of the extruder: 235°C; the temperature of the casting machine: 30°C; the longitudinal stretch ratio: 510%; Longitudinal stretching preheating temperature: 125°C; longitudinal stretching temperature: 110°C; transverse stretching ratio: 930%; transverse stretching preheating temperature: 180°C; transverse stretching temperatu
PUM
Property | Measurement | Unit |
---|---|---|
Total thickness | aaaaa | aaaaa |
Thickness | aaaaa | aaaaa |
Layer thickness | aaaaa | aaaaa |
Abstract
Description
Claims
Application Information
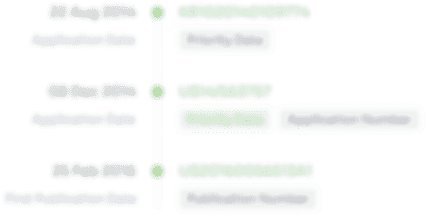
- R&D Engineer
- R&D Manager
- IP Professional
- Industry Leading Data Capabilities
- Powerful AI technology
- Patent DNA Extraction
Browse by: Latest US Patents, China's latest patents, Technical Efficacy Thesaurus, Application Domain, Technology Topic.
© 2024 PatSnap. All rights reserved.Legal|Privacy policy|Modern Slavery Act Transparency Statement|Sitemap