Manufacturing method for large-caliber abrasion-resistant corrosion-resistant ternary composite pipe accessory
A ternary composite and manufacturing method technology, applied in the direction of pipes/pipe joints/pipes, pipes, branch pipelines, etc., can solve the problems of waste of raw materials, high labor cost, low processing efficiency, etc., and achieve smooth and smooth surface and long service life. Guaranteed, quality assurance effect
- Summary
- Abstract
- Description
- Claims
- Application Information
AI Technical Summary
Benefits of technology
Problems solved by technology
Method used
Image
Examples
Embodiment 1
[0045] Embodiment 1: For DN600 equal-diameter right-angle tee pipe (see figure 1 , figure 2 ) to make this method (unspecified units are mm, the same below)
[0046] a. Fabrication of metal-ceramic composite pipe DN600 equal-diameter right-angle tee fittings
[0047] Cut the metal-ceramic composite steel pipe with an outer diameter of 630, a steel pipe wall thickness of 12, and a ceramic layer thickness of 6, grind and splice it into the required tee, and form it by electric welding. The three-port flange is installed and welded by electric welding. The side lengths from the center of the three-way pipe fitting to the three ports are the same, both a=b=c=500, and a and b are on the same straight line, so this straight line segment is selected as the axis for rotation during resin casting.
[0048] b. Fitting joint bridging
[0049] The internal joints of ceramic composite tee pipe fittings are made up with wear-resistant materials. The wear-resistant materials are mainly com
Embodiment 2
[0060] Example 2: For DN1000-DN600 different diameter 60 degree oblique tee pipe (see Figure 7 , Figure 8 ) to make this method (unspecified units are mm, the same below)
[0061] a. Metal-ceramic composite pipe DN1000-DN600 different diameter 60 degree oblique tee pipe fittings production
[0062] Cut metal-ceramic composite steel pipes with an outer diameter of 1020, a steel pipe wall thickness of 14, and a ceramic layer thickness of 6, and a metal-ceramic composite steel pipe with an outer diameter of 630, a steel pipe wall thickness of 12, and a ceramic layer thickness of 5, grind and splice them into required tees, and form them by electric welding , the three ports are installed with flanges and welded by electric welding, the side lengths from the center of the pipe fitting to the three ports are a=400 b =950 c=950, and the pipe sections a and b are on the same straight line, so when casting resin, choose this straight line section as axis to rotate.
[0063] b. Fitti
PUM
Property | Measurement | Unit |
---|---|---|
Granularity | aaaaa | aaaaa |
Abstract
Description
Claims
Application Information
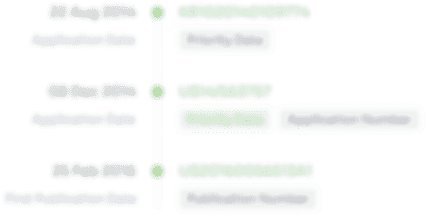
- R&D Engineer
- R&D Manager
- IP Professional
- Industry Leading Data Capabilities
- Powerful AI technology
- Patent DNA Extraction
Browse by: Latest US Patents, China's latest patents, Technical Efficacy Thesaurus, Application Domain, Technology Topic.
© 2024 PatSnap. All rights reserved.Legal|Privacy policy|Modern Slavery Act Transparency Statement|Sitemap