Preparation method of low-carbon aluminum-carbon refractory material for use in continuous casting
A technology of refractory material and low carbon aluminum, applied in the field of refractory materials, can solve the problems of difficult dispersion, high temperature strength of refractory materials, limited improvement in oxidation resistance and slag erosion resistance, etc., and achieves low decarburization layer thickness, small erosion Depth, the effect of improving high temperature strength
- Summary
- Abstract
- Description
- Claims
- Application Information
AI Technical Summary
Benefits of technology
Problems solved by technology
Method used
Examples
Embodiment 1
[0027] In this example, 5% polyborosilazane by mass is added to the phenolic resin. After mixing evenly, it is added to the aluminum-carbon refractory raw material. In the aluminum-carbon refractory raw material, alumina is 94wt%, graphite is 6wt%, and phenolic resin is added. , is 6wt% of the weight of the aluminum-carbon refractory raw material. After kneading, 120MPa pressure isostatic pressing, under nitrogen atmosphere (nitrogen content greater than 99.99%), heated to 1200°C at a heating rate of 1°C / min, and kept for 5 hours.
Embodiment 2
[0029] In this example, 7% polyborosilazane by mass is added to the phenolic resin. After mixing evenly, it is added to the aluminum-carbon refractory raw material. In the aluminum-carbon refractory raw material, alumina is 94wt%, graphite is 6wt%, and phenolic resin is added , is 6wt% of the weight of the aluminum-carbon refractory raw material. After kneading, 120MPa pressure isostatic pressing, under nitrogen atmosphere (nitrogen content greater than 99.99%), heated to 1200°C at a heating rate of 1°C / min, and kept for 5 hours.
Embodiment 3
[0031] In this example, 5% polyborosilazane by mass is added to the phenolic resin. After mixing evenly, it is added to the raw material of aluminum-carbon refractory material. In the raw material of aluminum-carbon refractory material, alumina is 97wt%, graphite is 3wt%, and phenolic resin is added , which is 4wt% of the weight of the aluminum-carbon refractory raw material. After kneading, 120MPa pressure isostatic pressing, under nitrogen atmosphere (nitrogen content greater than 99.99%), heated to 1200°C at a heating rate of 1°C / min, and kept for 5 hours.
PUM
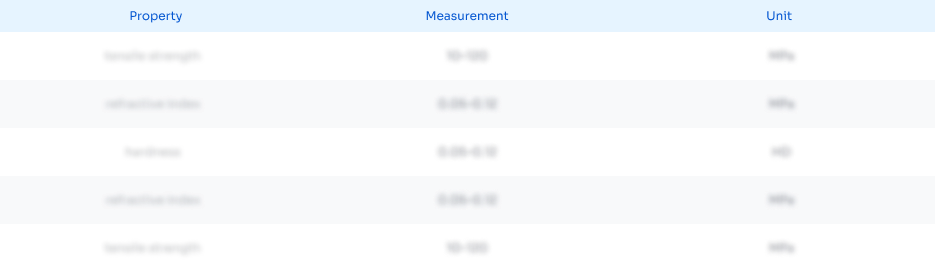
Abstract
Description
Claims
Application Information
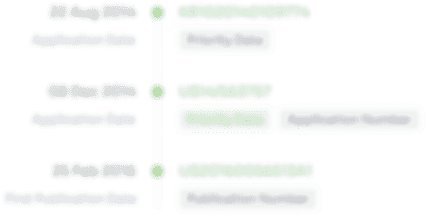
- R&D Engineer
- R&D Manager
- IP Professional
- Industry Leading Data Capabilities
- Powerful AI technology
- Patent DNA Extraction
Browse by: Latest US Patents, China's latest patents, Technical Efficacy Thesaurus, Application Domain, Technology Topic.
© 2024 PatSnap. All rights reserved.Legal|Privacy policy|Modern Slavery Act Transparency Statement|Sitemap