Anti-corrosion acrylic acid epoxy resin powder paint for ceramic
A technology of acrylic epoxy resin and powder coating, which is applied in the direction of powder coating, anti-corrosion coating, coating, etc., and can solve the problems of low hardness, non-corrosion resistance, poor stain resistance, etc.
- Summary
- Abstract
- Description
- Claims
- Application Information
AI Technical Summary
Benefits of technology
Problems solved by technology
Method used
Examples
Embodiment 1
[0014] A corrosion-resistant acrylic epoxy resin powder coating for ceramics, its raw materials are proportioned in parts by weight as follows: 100 parts of glycidyl methacrylate; 30 parts of polyhydric alcohol; 5 parts of azobisisobutyronitrile; 15 parts of monobasic acid ; 1 part of di-tert-butyl peroxide; 5 parts of dicyclopentadiene; 5 parts of benzophenone; 5 parts of maleic anhydride; 10 parts of epoxy resin; 5 parts of zinc oxide; polydimethylsiloxane 1 part of alkane; 1 part of 1-o-tolylformin; 15 parts of dodecanedioic acid; 1 part of 2-mercaptobenzothiazole; 45 parts of titanium dioxide.
[0015] Put the above raw materials into the reaction kettle, raise the temperature to 140°C, keep warm for 6 hours and mix evenly, after cooling, pulverize with a pulverizer, and sieve with a 150mg sieve to prepare the coating.
[0016] The product has a melting point of 200°C and a density of 135g / cm 3 , soaked in 5% hydrochloric acid solution for 20 days without exception; gloss
Embodiment 2
[0018] A corrosion-resistant acrylic epoxy resin powder coating for ceramics, its raw materials are proportioned in parts by weight as follows: 100 parts of glycidyl methacrylate; 40 parts of polyol; 15 parts of azobisisobutyronitrile; 25 parts of monobasic acid ; 10 parts of di-tert-butyl peroxide; 15 parts of dicyclopentadiene; 15 parts of benzophenone; 25 parts of maleic anhydride; 30 parts of epoxy resin; 15 parts of zinc oxide; modified polyether polyester 10 parts of organosiloxane; 10 parts of 1-o-tolylformin; 35 parts of dodecanedioic acid; 5 parts of 2-mercaptobenzothiazole; 55 parts of titanium dioxide.
[0019] Put the above raw materials into the reaction kettle, raise the temperature to 180°C, keep warm for 10 hours and mix evenly, after cooling, pulverize with a pulverizer, and sieve with a 150mg sieve to prepare the coating.
[0020] The product has a melting point of 210°C and a density of 140g / cm 3 , no abnormality after soaking in 5% hydrochloric acid solutio
Embodiment 3
[0022] A kind of corrosion-resistant acrylic epoxy resin powder coating for ceramics, its raw material ratio by weight is as follows: 100 parts of glycidyl methacrylate; 35 parts of polyhydric alcohol; 10 parts of azobisisobutyronitrile; 20 parts of monobasic acid ; 5 parts of di-tert-butyl peroxide; 10 parts of dicyclopentadiene; 10 parts of azodicyanovaleric acid initiator; 15 parts of maleic anhydride; 20 parts of epoxy resin; 10 parts of zinc oxide; 5 parts of ether polyester modified organosiloxane; 5 parts of 1-o-tolylformin; 25 parts of dodecanedioic acid; 3 parts of 2-mercaptobenzothiazole; 50 parts of titanium dioxide.
[0023] Put the above raw materials into the reaction kettle, heat up to 160°C, keep warm for 8 hours and mix evenly, after cooling, pulverize with a pulverizer, and sieve with a 150mg sieve to prepare the coating.
[0024] The product has a melting point of 220°C and a density of 145g / cm 3 , no abnormality after soaking in 5% hydrochloric acid solutio
PUM
Property | Measurement | Unit |
---|---|---|
Melting point | aaaaa | aaaaa |
Density | aaaaa | aaaaa |
Melting point | aaaaa | aaaaa |
Abstract
Description
Claims
Application Information
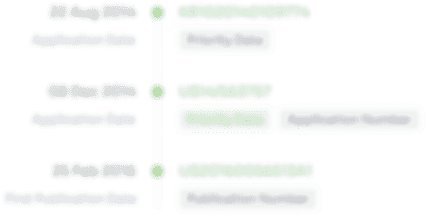
- R&D Engineer
- R&D Manager
- IP Professional
- Industry Leading Data Capabilities
- Powerful AI technology
- Patent DNA Extraction
Browse by: Latest US Patents, China's latest patents, Technical Efficacy Thesaurus, Application Domain, Technology Topic.
© 2024 PatSnap. All rights reserved.Legal|Privacy policy|Modern Slavery Act Transparency Statement|Sitemap