Method for producing chromate by liquid-phase catalytic oxidation of chromite
A liquid-phase catalysis and chromate technology, applied in the direction of chromate/dichromate, etc., can solve the problems of long reaction time and disadvantages
- Summary
- Abstract
- Description
- Claims
- Application Information
AI Technical Summary
Problems solved by technology
Method used
Examples
Embodiment 1
[0020] Chromite ore 250g, chromite ore particle size less than 50μm (-300 mesh), alkali ore ratio 4:1, alkali concentration 60%, manganese hydroxide 125g, lye, chromite and manganese hydroxide are prepared as raw material Slurry was added to the reaction kettle, oxygen was used as an oxidant, the total pressure was controlled to 3.2MPa, the stirring speed was 650 rpm, the temperature was 260°C, the reaction was 120min, and the chromite leaching rate was 90.37%.
Embodiment 2
[0024] 250g of chromite, the particle size of chromite is less than 28μm (500 mesh), the alkali ore ratio is 4:1, the alkali concentration is 60%, manganese hydroxide 12g, the lye, chromite and manganese hydroxide are prepared into slurry , into the reactor, oxygen as an oxidant, control the total pressure of 3.2MPa, stirring speed of 650 rpm, temperature of 260 ° C, reaction 120min, chromite leaching rate of 57.64%.
Embodiment 3
[0028] 250g of chromite, the particle size of chromite is less than 50μm (-300 mesh), the ratio of alkali to mineral is 4:1, the concentration of alkali is 60%, copper oxide is 15g, and lye, chromite and copper oxide are prepared into slurry, Adding oxygen into the reaction kettle, using oxygen as an oxidant, controlling the total pressure to 3.2MPa, stirring speed to 650 rpm, temperature to 260°C, and reacting for 120 minutes, the leaching rate of chromite was 82.53%.
PUM
Property | Measurement | Unit |
---|---|---|
Granularity | aaaaa | aaaaa |
Abstract
Description
Claims
Application Information
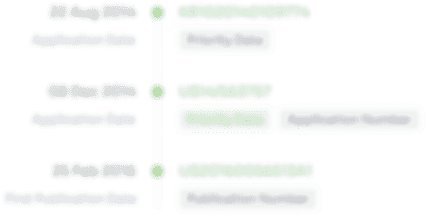
- R&D Engineer
- R&D Manager
- IP Professional
- Industry Leading Data Capabilities
- Powerful AI technology
- Patent DNA Extraction
Browse by: Latest US Patents, China's latest patents, Technical Efficacy Thesaurus, Application Domain, Technology Topic.
© 2024 PatSnap. All rights reserved.Legal|Privacy policy|Modern Slavery Act Transparency Statement|Sitemap