Foam coating grinding tool and preparing method thereof
An abrasive tool and foam technology is applied in the field of coated foam abrasive tool and its preparation. Good heat dissipation effect
- Summary
- Abstract
- Description
- Claims
- Application Information
AI Technical Summary
Problems solved by technology
Method used
Image
Examples
Embodiment 1
[0034]A kind of coated foam abrasive tool, comprising latex paper base layer, ethylene-vinyl acetate copolymer hot melt adhesive type primer layer and a foam layer with a thickness of 1mm, the foam layer is obtained by foaming ethylene-vinyl acetate copolymer resin liquid The silicon carbide abrasive used for grinding is evenly embedded in the resin foam;
[0035] The preparation method of above-mentioned coated foam abrasive tool, comprises the following steps:
[0036] 1. Substrate pretreatment: Latex paper can be used directly as a substrate;
[0037] 2. Primer: Ethylene-vinyl acetate copolymer hot-melt adhesive can be cast on the latex paper substrate through a hot-melt machine to form a primer layer;
[0038] 3. Casting and foaming: the foam layer is obtained by mixing ethylene-vinyl acetate copolymer resin and silicon carbide abrasive and then casting and foaming;
[0039] First, prepare the foam layer slurry by mass parts by 100 parts of ethylene-vinyl acetate copolymer
Embodiment 2
[0044] A coated foam abrasive tool, comprising a kraft paper base layer, a polyisobutylene rubber hot-melt adhesive primer layer and a foam layer with a thickness of 1 mm, the foam layer is obtained by foaming an ethylene-vinyl acetate copolymer resin solution, and can be used for grinding The active silicon carbide abrasive is evenly embedded in the resin foam;
[0045] The preparation method of above-mentioned coated foam abrasive tool, comprises the following steps:
[0046] 1. Substrate pretreatment: kraft paper is used as a substrate after waterproofing;
[0047] 2. Primer: Polyisobutylene rubber hot-melt adhesive can be cast on the kraft paper substrate through a hot-melt machine to form a primer layer;
[0048] 3. Casting and foaming: the foam layer is obtained by mixing ethylene-vinyl acetate copolymer resin and silicon carbide abrasive and then casting and foaming;
[0049] First, prepare the foam layer slurry, by mass parts, 100 parts of ethylene-vinyl acetate copolym
Embodiment 3
[0054] A coated foam abrasive tool, comprising a polyester film base layer, a polyester hot-melt adhesive primer layer and a foam layer with a thickness of 3mm, the foam layer is obtained by foaming polyvinyl alcohol resin liquid, and plays a grinding role Silicon carbide abrasive is evenly embedded in the resin foam;
[0055] The preparation method of above-mentioned coated foam abrasive tool, comprises the following steps:
[0056] 1. Substrate pretreatment: polyester film can be used directly as a substrate;
[0057] 2. Primer: Polyester hot-melt adhesive can be cast on the substrate by a hot-melt machine to form a primer layer;
[0058] 3. Casting and foaming: the foam layer is obtained by mixing polyvinyl alcohol resin and silicon carbide abrasives and then casting and foaming;
[0059] First, prepare the foam layer slurry, by mass parts, 100 parts of polyvinyl alcohol resin, 80 parts of N,N-dimethylformamide, 0.01 part of sodium dodecylbenzene sulfonate antistatic agent,
PUM
Property | Measurement | Unit |
---|---|---|
Thickness | aaaaa | aaaaa |
Thickness | aaaaa | aaaaa |
Thickness | aaaaa | aaaaa |
Abstract
Description
Claims
Application Information
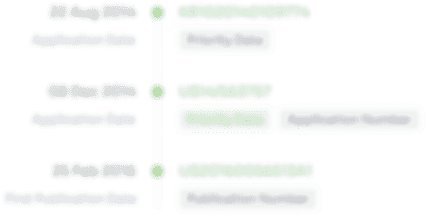
- R&D Engineer
- R&D Manager
- IP Professional
- Industry Leading Data Capabilities
- Powerful AI technology
- Patent DNA Extraction
Browse by: Latest US Patents, China's latest patents, Technical Efficacy Thesaurus, Application Domain, Technology Topic.
© 2024 PatSnap. All rights reserved.Legal|Privacy policy|Modern Slavery Act Transparency Statement|Sitemap