Composite phase change material for LED thermal interface and preparation method thereof
A composite phase change material and thermal interface technology, applied in heat exchange materials, chemical instruments and methods, etc., can solve problems such as inability to effectively reduce contact thermal resistance, small thermal conductivity, and narrow phase transition temperature threshold, and achieve phase change. The effect of wide temperature change threshold, high thermal conductivity and large phase change enthalpy
- Summary
- Abstract
- Description
- Claims
- Application Information
AI Technical Summary
Problems solved by technology
Method used
Examples
preparation example Construction
[0031] A method for preparing a composite phase-change material for an LED thermal interface, the steps of which are:
[0032] 1) Material preparation: mix all raw materials evenly;
[0033] 2) Sample preparation: Melt the uniformly mixed raw materials above under a protective atmosphere, and then cool to room temperature.
[0034] Preferably, step 2) is specifically: put the mixed raw materials into the smelting furnace and pass in protective gas, raise the temperature from room temperature to 600-800°C, then keep it warm for 20min-1h, then turn off the heating power and cool down to room temperature naturally.
[0035] The protective gas is at least one of nitrogen, helium, neon, argon and xenon.
[0036] Preferably, step 2) specifically includes: putting the mixed raw materials into a smelting furnace and introducing a protective gas, raising the temperature from room temperature to 700°C, keeping the temperature for 30 minutes, and then turning off the heating power and cool
Embodiment 1
[0039] Preparation of raw materials: Take various raw material powders with a purity of more than 99.9%, in terms of mass percentage, 44.51% bismuth, 17.47% tin, 35.77% indium, 0.55% antimony, and 1.7% colloidal graphite powder, add them to a corundum crucible, mix and stir. Sample preparation: Turn on the power switch of the heating and melting furnace, put the mixed raw materials into the melting furnace and pass nitrogen gas, raise the temperature of the melting furnace from room temperature to 700°C in 2.5 hours, then keep at 700°C for half an hour, and then turn off the heating Naturally cool to room temperature after power on.
[0040] The melting point of the thermal interface material prepared in this example was tested by DSC-Q20, and the obtained test result was: 78.9°C.
Embodiment 2
[0042] Preparation of raw materials: Take various raw material powders with a purity of more than 99.9%, by mass percentage, bismuth 34.75%, tin 13.47%, indium 49.53%, antimony 0.55%, colloidal graphite powder 1.7%, add to a corundum crucible, mix and stir. The sample preparation process is the same as in Example 1.
[0043] The melting point of the thermal interface material prepared in this example was tested by DSC-Q20, and the obtained test result was: 61.6°C.
PUM
Property | Measurement | Unit |
---|---|---|
Thermal conductivity | aaaaa | aaaaa |
Abstract
Description
Claims
Application Information
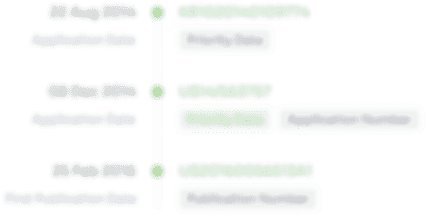
- R&D Engineer
- R&D Manager
- IP Professional
- Industry Leading Data Capabilities
- Powerful AI technology
- Patent DNA Extraction
Browse by: Latest US Patents, China's latest patents, Technical Efficacy Thesaurus, Application Domain, Technology Topic.
© 2024 PatSnap. All rights reserved.Legal|Privacy policy|Modern Slavery Act Transparency Statement|Sitemap