System and method for gas direct heating
A coal gas and direct technology, applied in the field of coal chemical industry, can solve problems such as inability to guarantee flue gas, blockage, high risk, etc., and achieve the effect of reducing the risk of explosion, simple process method, and low operating cost
- Summary
- Abstract
- Description
- Claims
- Application Information
AI Technical Summary
Problems solved by technology
Method used
Examples
Example Embodiment
[0022] Example 1
[0023] by figure 1 It can be seen that the direct gas heating system of this embodiment is composed of an incinerator 1 and a first combustion regenerative heating furnace 2 and a second combustion regenerative heating furnace 3 connected by pipelines and control valves.
[0024] The incinerator 1 of this embodiment is mainly used to preheat the air and combust the combustible gases in the flue gas. The incinerator 1 includes an air inlet, a flue gas inlet, an air outlet, and a flue gas outlet. The air pipe is connected to introduce the outside air into the system, the flue gas outlet is connected to the outside flue gas dust removal system through the pipe, the air outlet and the flue gas inlet are respectively connected to the air inlet and flue gas outlet of the two combustion regenerative heating furnaces through the pipe .
[0025] The combustion regenerative heating furnace of this embodiment includes a first combustion regenerative heating furnace 2 and a seco
Example Embodiment
[0035] Example 2
[0036] There is one combustion regenerative heating furnace in this embodiment, and its specific structure is the same as that of the first combustion regenerative heating furnace 2 in Example 1. The specific connection method is: the combustion regenerative heating furnace includes a furnace Body 2-1, a feed inlet and a flue gas outlet are processed on the top of the furnace body 2-1, and an automatic coking machine 2-2 is installed on the feed inlet, which is connected to the lump coal discharge pipeline and passes through the automatic coking machine 2-2 Fill the furnace body 2-1 with half coke. A vent pipe is installed on the flue gas outlet. The vent pipe is connected to the flue gas pipe and the gas pipe through a T-shaped joint. A flue gas control valve is installed on the flue gas pipe. The valve adopts a common commercially available flapper valve. The flue gas control valve is in communication with the flue gas inlet of the incinerator 1. A gas inlet v
Example Embodiment
[0042] Example 3
[0043] There are 4 combustion regenerative heating furnaces in this embodiment, including the first combustion regenerative heating furnace 2, the second combustion regenerative heating furnace 3, the third combustion regenerative heating furnace, and the fourth combustion regenerative heating furnace. Four combustion regenerative heating furnaces are connected in parallel to each pipeline. The connection method of each combustion regenerative heating furnace is the same as the connection method of the first combustion regenerative heating furnace 2 in Example 1 above. Other control valves and others The components are the same as in Example 1.
[0044] The method of using this system to realize gas heating is the same as that of the above-mentioned embodiment 1, except that the four combustion regenerative heating furnaces are switched and operated continuously to ensure that the total gas volume remains unchanged.
[0045] The combustion temperature of the semi-cok
PUM
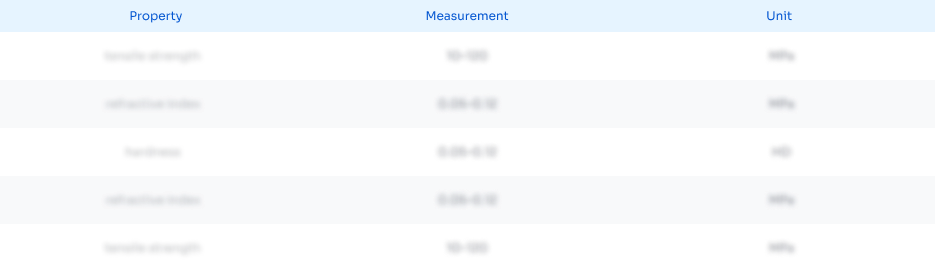
Abstract
Description
Claims
Application Information
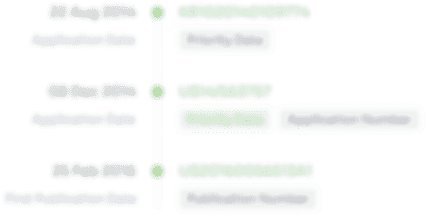
- R&D Engineer
- R&D Manager
- IP Professional
- Industry Leading Data Capabilities
- Powerful AI technology
- Patent DNA Extraction
Browse by: Latest US Patents, China's latest patents, Technical Efficacy Thesaurus, Application Domain, Technology Topic.
© 2024 PatSnap. All rights reserved.Legal|Privacy policy|Modern Slavery Act Transparency Statement|Sitemap