Method for combined production of ethyl methyl ketone and ethanol
A technology for methyl ethyl ketone and ethanol, applied in the field of co-production of methyl ethyl ketone and ethanol, can solve problems such as potential safety hazards, waste of hydrogen resources, etc., and achieve the effects of high production income, cost reduction, and good technical effect
- Summary
- Abstract
- Description
- Claims
- Application Information
AI Technical Summary
Problems solved by technology
Method used
Examples
Example Embodiment
[0018] [Example 1]
[0019] Preparation of CuO-ZnO-ZrO by Co-precipitation 2 Hydrogenation industrial catalyst (cylindrical, Φ5*5mm), with CuO content 65wt%, ZnO content 25wt%, ZrO 2 Content 10wt%. The CuO-ZnO-MgO dehydrogenation industrial catalyst (cylindrical, Φ5*5mm) was prepared by co-precipitation method, wherein the CuO content was 60wt%, the ZnO content was 25wt%, and the MgO content was 15wt%. The hydrogenation reactor and the dehydrogenation reactor are both 316 stainless steel tubes, with an inner diameter of 38mm, the hydrogenation catalyst loading amount is 9Kg, and the dehydrogenation reactor catalyst loading amount is 0.4Kg. The sec-butyl acetate enters the hydrogenation reactor, and the hydrogenation reaction product is separated by a rectifying tower; after separation, the sec-butanol enters the dehydrogenation reactor, and the hydrogen produced by the dehydrogenation reactor is pressurized by a supercharger, and then mixed with the hydrogenation raw materials.
Example Embodiment
[0023] [Example 2]
[0024] According to the conditions and steps described in Example 1, the hydrogenation catalyst prepared by the co-precipitation method is CuO-CaO-SiO 2 (cylindrical, Φ5*5mm), with CuO content 60wt%, CaO content 10wt%, SiO 2 Content 30wt%. Preparation of CuO-K by Co-precipitation 2 O-SiO 2 Dehydrogenation industrial catalyst (cylindrical, Φ5*5mm), of which CuO content is 55wt%, SiO 2 Content 40wt%, K 2 The O content was 5 wt%. The hydrogenation catalyst loading amount is 4Kg, and the dehydrogenation reactor catalyst loading amount is 1.8Kg.
[0025] Hydrogenation reaction conditions: the molar ratio of sec-butyl acetate raw material and hydrogen is 20; the liquid hourly space velocity of sec-butyl acetate raw material mass is 2.0h -1 ; The reaction temperature is 220°C; the reaction pressure is 2.0MPaG.
[0026] Dehydrogenation reaction conditions: sec-butanol mass liquid hourly space velocity of 3.0h -1 ; The reaction temperature is 200°C; the reactio
Example Embodiment
[0028] [Example 3]
[0029] According to the conditions and steps described in Example 1, the hydrogenation catalyst prepared by the co-precipitation method is CuO-ZnO-Al 2 O 3 -MnO 2 (cylindrical, Φ5*5mm), with CuO content 60wt%, ZnO content 15wt%, MnO 2 3wt%, Al 2 O 3 22wt%. Preparation of CuO-La by Impregnation Method 2 O 3 -CaO-Al 2 O 3 Dehydrogenation industrial catalyst (spherical, Φ5mm), in which CuO content is 15wt%, La 2 O 3 Content 2wt%, Al 2 O 3 Content 80wt%, CaO3wt%. The hydrogenation catalyst loading amount is 4Kg, and the dehydrogenation reactor catalyst loading amount is 1.2Kg.
[0030] Hydrogenation reaction conditions: the molar ratio of sec-butyl acetate raw material and hydrogen is 30; the mass liquid hourly space velocity of sec-butyl acetate raw material is 4.5h -1 ; The reaction temperature is 240°C; the reaction pressure is 8.0MPaG.
[0031] Dehydrogenation reaction conditions: sec-butanol mass liquid hourly space velocity of 10.0h -1 ; Th
PUM
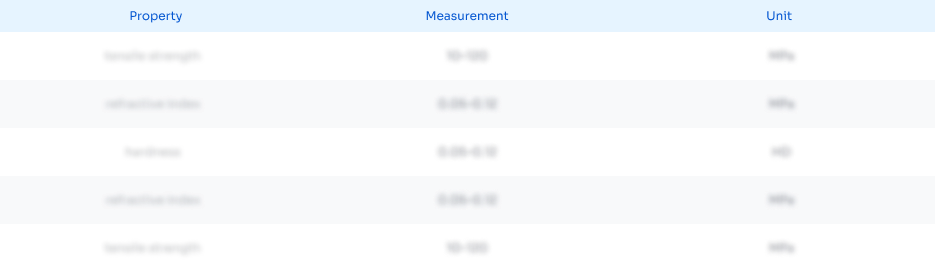
Abstract
Description
Claims
Application Information
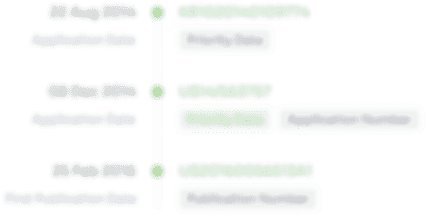
- R&D Engineer
- R&D Manager
- IP Professional
- Industry Leading Data Capabilities
- Powerful AI technology
- Patent DNA Extraction
Browse by: Latest US Patents, China's latest patents, Technical Efficacy Thesaurus, Application Domain, Technology Topic.
© 2024 PatSnap. All rights reserved.Legal|Privacy policy|Modern Slavery Act Transparency Statement|Sitemap