Abrasion resistant steel plate having low-temperature toughness and hydrogen embrittlement resistance, and manufacturing method therefor
A technology of low temperature toughness and manufacturing method, applied in the field of wear-resistant thick steel plates and suitable steel plates, can solve the problems of low temperature toughness and hydrogen embrittlement resistance, steel cracking and other problems, and achieve the effect of excellent low temperature toughness and hydrogen embrittlement resistance.
- Summary
- Abstract
- Description
- Claims
- Application Information
AI Technical Summary
Problems solved by technology
Method used
Image
Examples
Embodiment
[0102] Steels A to K having the chemical compositions shown in Table 1 were melted and slabs were cast, and thick steel plates were produced under the conditions shown in Table 2. The temperature measurement of the plate was carried out with a thermocouple inserted into the central part of the plate thickness.
[0103] The microstructure of the steel sheet, the average grain size of crystal grains surrounded by high-angle grain boundaries with a misorientation of 15° or more, the density of fine precipitates with a diameter of 50 nm or less, the Brinell hardness of the obtained steel sheet, and the summer temperature at -40°C The specific impact absorption energy and delayed failure safety index are shown in Table 2.
[0104] The structure of the steel plate can be determined as follows: collect a sample of a cross-section perpendicular to the rolling direction, grind the cross-section to a mirror surface, corrode it with a nitric acid methanol solution, and use an optical micros
PUM
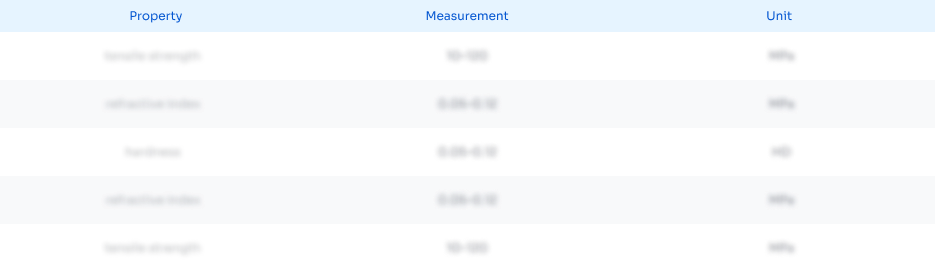
Abstract
Description
Claims
Application Information
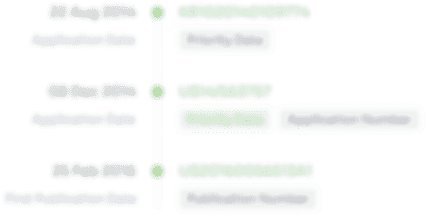
- R&D Engineer
- R&D Manager
- IP Professional
- Industry Leading Data Capabilities
- Powerful AI technology
- Patent DNA Extraction
Browse by: Latest US Patents, China's latest patents, Technical Efficacy Thesaurus, Application Domain, Technology Topic.
© 2024 PatSnap. All rights reserved.Legal|Privacy policy|Modern Slavery Act Transparency Statement|Sitemap