Method for producing environmentally friendly high-temperature fold-resistant high-strength high purity corundum bricks
A technology of flexural strength and corundum bricks is applied in the field of refractory materials, which can solve the problems of high cost, high content of nano-powder and high firing temperature, and achieve the effects of short holding time, low firing temperature and simple preparation process.
- Summary
- Abstract
- Description
- Claims
- Application Information
AI Technical Summary
Benefits of technology
Problems solved by technology
Method used
Examples
Embodiment 1
[0024] The production method of high-purity corundum bricks with high temperature and high bending strength for environmental protection:
[0025] (1) Raw material preparation:
[0026] A particles: fused corundum particles with a particle size of 3 mm;
[0027] B particles: fused corundum particles with a particle size of 1mm;
[0028] C particles: titanium dioxide micropowder with a particle size of 9 μm;
[0029] D particles: particle size D 50 = 2.5μm, α-Al with a mass fraction of 99.65% 2 o 3 Micropowder;
[0030] E particles: α-Al with an average particle size of 200nm and a mass fraction of 99.9% 2 o 3 Nano powder;
[0031] F particles: fine powder of limestone with a particle size of 10 μm;
[0032] (2) Forming of batching brick body:
[0033] In terms of parts by weight, 50 parts of granule A, 12 parts of granule B, 0.1 part of granule C, 5 parts of granule D, 0.2 part of granule E, and 0.5 part of granule F are mixed and batched, put into a mixing machine, and
Embodiment 2
[0039] The production method of high-purity corundum bricks with high temperature and high bending strength for environmental protection:
[0040] (1) Raw material preparation:
[0041] A particles: fused corundum particles with a particle size of 3mm;
[0042] B particles: fused corundum particles with a particle size of 2mm;
[0043] C particles: titanium dioxide micropowder with a particle size of 5 μm;
[0044] D particles: particle size D 50 = 2.5μm, α-Al with a mass fraction of 99.65% 2 o 3 Micropowder;
[0045] E particles: α-Al with an average particle size of 250nm and a mass fraction of 99.9% 2 o 3 Nano powder;
[0046] F particles: fine powder of limestone with a particle size of 8 μm;
[0047] (2) Forming of batching brick body:
[0048] In terms of parts by weight, 52 parts of granule A, 8 parts of granule B, 0.1 part of granule C, 6 parts of granule D, 0.2 part of granule E, and 0.4 part of granule F are mixed and batched, put into a mixing machine, and a
Embodiment 3
[0054] The production method of high-purity corundum bricks with high temperature and high bending strength for environmental protection:
[0055] (1) Raw material preparation:
[0056] A particles: fused corundum particles with a particle size of 3mm;
[0057] B particles: fused corundum particles with a particle size of 1mm;
[0058] C particles: titanium dioxide micropowder with a particle size of 8 μm;
[0059] D particles: particle size D 50 = 2.5μm, α-Al with a mass fraction of 99.65% 2 o 3 Micropowder;
[0060] E particles: α-Al with an average particle size of 210nm and a mass fraction of 99.9% 2 o 3 Nano powder;
[0061] F Particles: Limestone powder with a particle size of 9 μm;
[0062] (2) Forming of batching brick body:
[0063] In parts by weight, 51 parts of granule A, 11 parts of granule B, 0.1 part of granule C, 5 parts of granule D, 0.2 part of granule E, and 0.5 part of granule F are mixed and batched, put into a mixing machine, and a binder is added
PUM
Property | Measurement | Unit |
---|---|---|
Granularity | aaaaa | aaaaa |
Granularity | aaaaa | aaaaa |
Granularity | aaaaa | aaaaa |
Abstract
Description
Claims
Application Information
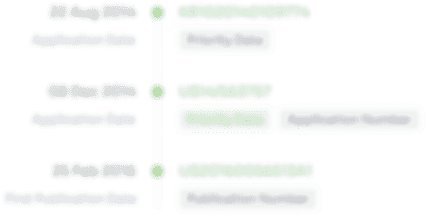
- R&D Engineer
- R&D Manager
- IP Professional
- Industry Leading Data Capabilities
- Powerful AI technology
- Patent DNA Extraction
Browse by: Latest US Patents, China's latest patents, Technical Efficacy Thesaurus, Application Domain, Technology Topic.
© 2024 PatSnap. All rights reserved.Legal|Privacy policy|Modern Slavery Act Transparency Statement|Sitemap