Ultra-precision machining method for gallium oxide substrate
An ultra-precision machining and gallium oxide technology, which is applied in metal processing equipment, manufacturing tools, grinding devices, etc., can solve the problems of high cost of consumables, no consideration of cleavage of crystal materials, and no cleavage of sapphire, etc., to achieve processing The effect of cost reduction, avoiding processing difficulty and rising processing cost
- Summary
- Abstract
- Description
- Claims
- Application Information
AI Technical Summary
Benefits of technology
Problems solved by technology
Method used
Image
Examples
Embodiment Construction
[0027] The present invention will be further described below in conjunction with specific embodiments.
[0028] figure 1 It is the process flow chart of traditional sapphire ultra-precision machining, figure 2 It is a process flow chart of the ultra-precision machining method for gallium oxide substrates of the present invention.
[0029] Abrasive particle size classification representation method: particle size number "W", particle size unit "micron"; abrasive particle size increases with the increase in the value after "W", for example, W0.5 means that the abrasive particle size distribution is less than 0.5 micron Within the range, W1.5 means that the abrasive particle size distribution range is between 0.5 and 1.5 microns. In addition, the particle size number can also be expressed by "mesh". The abrasive particle size becomes smaller with the increase of the "mesh" value. There are different standards for screen specifications in different countries and industries, so the
PUM
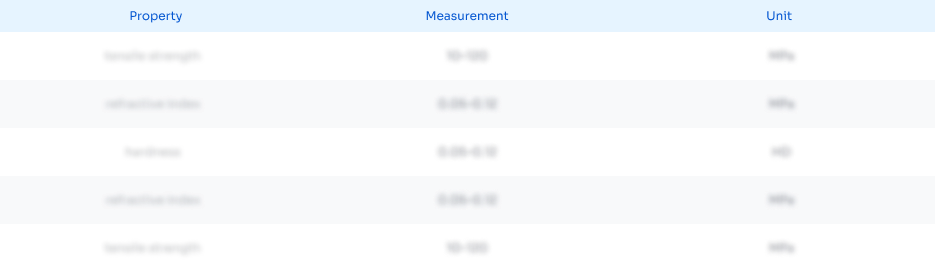
Abstract
Description
Claims
Application Information
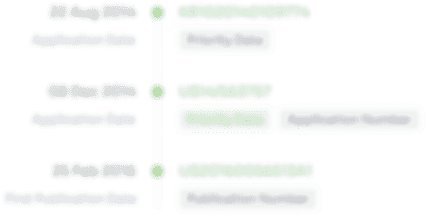
- R&D Engineer
- R&D Manager
- IP Professional
- Industry Leading Data Capabilities
- Powerful AI technology
- Patent DNA Extraction
Browse by: Latest US Patents, China's latest patents, Technical Efficacy Thesaurus, Application Domain, Technology Topic.
© 2024 PatSnap. All rights reserved.Legal|Privacy policy|Modern Slavery Act Transparency Statement|Sitemap