Foamed heat insulation material and preparation method thereof
A thermal insulation material and foaming agent technology, applied in the field of foam thermal insulation material and its preparation, can solve the problems of high raw material cost and high production cost, and achieve the effect of simple process, high strength and good thermal insulation performance
- Summary
- Abstract
- Description
- Claims
- Application Information
AI Technical Summary
Problems solved by technology
Method used
Image
Examples
Embodiment 1
[0044] This embodiment relates to a foam insulation material, including the following raw materials in parts by weight: 40 parts of fly ash, 60 parts of discarded ordinary flat glass powder, 10 parts of borax, and 1 part of limestone;
[0045] The present embodiment also relates to the preparation method of the thermal insulation material, comprising the following steps: (the preparation flow chart is shown in figure 1 )
[0046] 1) Mix high-alumina fly ash, discarded ordinary flat glass powder, borax and limestone, add an equal amount of water and carry out wet grinding and mixing for 6-10 hours until the particle size of the material is 40-48 μm to obtain a slurry;
[0047] 2) drying the slurry at 100° C. to obtain a mixed powder, granulating, and then adopting a dry pressing method to press and form at 15 MPa to obtain a green body;
[0048] 3) Put the green body into a high-temperature furnace with a heating rate of 3°C / min, sinter at 850°C for 0.5h, and cool down to room
Embodiment 2
[0050] This embodiment relates to a foam insulation material, including the following raw materials in parts by weight: 45 parts of fly ash, 55 parts of discarded ordinary flat glass powder, 20 parts of borax, and 0.5 part of limestone;
[0051] The present embodiment also relates to a preparation method of the thermal insulation material, comprising the steps of:
[0052] 1) Mix high-alumina fly ash, discarded ordinary flat glass powder, borax and limestone, add an equal amount of water and carry out wet grinding and mixing for 6-10 hours until the particle size of the material is 35-40 μm to obtain a slurry;
[0053]2) drying the slurry at 120° C. to obtain a mixed powder, granulating, and then adopting a dry pressing method to press and form at 14 MPa to obtain a green body;
[0054] 3) Put the green body into a high-temperature furnace with a heating rate of 5°C / min, sinter at 800°C for 1 hour, and cool down to room temperature with the furnace, then cut off the irregular e
Embodiment 3
[0056] This embodiment relates to a foam insulation material, including the following raw materials in parts by weight: 50 parts of fly ash, 50 parts of discarded ordinary flat glass powder, 30 parts of borax, and 1.5 parts of limestone;
[0057] The present embodiment also relates to a preparation method of the thermal insulation material, comprising the steps of:
[0058] 1) Mix high-alumina fly ash, discarded ordinary flat glass powder, borax and limestone, add an equal amount of water and carry out wet grinding and mixing for 6-10 hours until the particle size of the material is 25-35 μm to obtain a slurry;
[0059] 2) drying the slurry at 110° C. to obtain a mixed powder, granulating, and then adopting a dry pressing method to press and form at 16 MPa to obtain a green body;
[0060] 3) Put the green body into a high-temperature furnace with a heating rate of 5°C / min, sinter at 900°C for 0.5h, and cool down to room temperature with the furnace, and then cut off the irregul
PUM
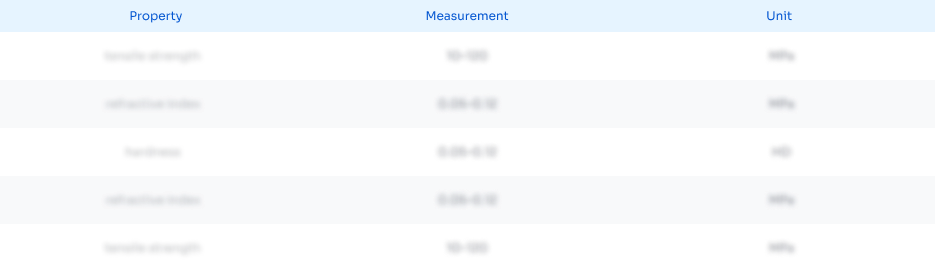
Abstract
Description
Claims
Application Information
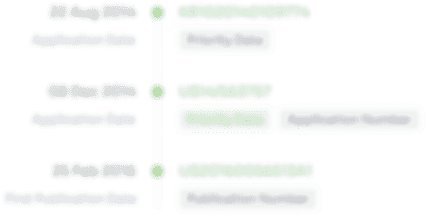
- R&D Engineer
- R&D Manager
- IP Professional
- Industry Leading Data Capabilities
- Powerful AI technology
- Patent DNA Extraction
Browse by: Latest US Patents, China's latest patents, Technical Efficacy Thesaurus, Application Domain, Technology Topic.
© 2024 PatSnap. All rights reserved.Legal|Privacy policy|Modern Slavery Act Transparency Statement|Sitemap