Method for preparing vanadium-nitrogen alloy with inactive vanadium pentoxide catalyst
The technology of vanadium pentoxide catalyst and vanadium nitrogen alloy is applied in the field of alloy preparation, which can solve the problems of unstable production, difficult storage of raw materials, strict temperature control requirements, etc., and achieve the effects of cost saving and simple operation.
- Summary
- Abstract
- Description
- Claims
- Application Information
AI Technical Summary
Benefits of technology
Problems solved by technology
Method used
Examples
example 1
[0017] First, weigh 150g of the vanadium pentoxide catalyst used for deactivation after the preparation of sulfuric acid, rinse it with clear water and dry it naturally, place it in a ball mill for ball milling and pass through a 150 mesh sieve to obtain ball milled particles, and then ball mill the particles Put it into a tube furnace for calcination, control the calcination temperature to 170°C, and after calcination for 55 minutes, let it stand for cooling to obtain pretreated vanadium pentoxide particles; then spread the pretreated vanadium pentoxide particles prepared above on the bottom of the crucible, Sprinkle a mixture of 80g ferric oxide powder and 250g aluminum oxide powder above the pretreated vanadium pentoxide particles, and then spread a layer of 0.7cm thick magnesium powder above the mixture; , insert an 8cm magnesium strip into the magnesium powder, ignite the magnesium strip and slowly feed nitrogen into the crucible at the same time, control the rate of nitrogen
example 2
[0019] First, weigh 120g of the vanadium pentoxide catalyst used for deactivation after the preparation of sulfuric acid, rinse it with clear water and dry it naturally, place it in a ball mill for ball milling and pass through a 150 mesh sieve to obtain ball milled particles, and then ball mill the particles Put it into a tube furnace for calcination, control the calcination temperature at 150°C, and after calcination for 45 minutes, let it stand for cooling to obtain pretreated vanadium pentoxide particles; then spread the pretreated vanadium pentoxide particles prepared above on the bottom of the crucible, Sprinkle a mixture of 70g ferric oxide powder and 200g aluminum oxide powder above the pretreated vanadium pentoxide particles, and then spread a layer of 0.5cm thick magnesium powder above the mixture; , insert a 7cm magnesium tape into the magnesium powder, ignite the magnesium tape and slowly feed nitrogen gas into the crucible at the same time, control the nitrogen gas fe
example 3
[0021] First, weigh 125g of the vanadium pentoxide catalyst used for deactivation after the preparation of sulfuric acid, rinse it with clear water and dry it naturally, place it in a ball mill for ball milling and pass through a 150 mesh sieve to obtain ball milled particles, and then ball mill the particles Put it into a tube furnace for calcination, control the calcination temperature to 160°C, and after calcination for 50 minutes, let it stand for cooling to obtain pretreated vanadium pentoxide particles; then spread the pretreated vanadium pentoxide particles prepared above on the bottom of the crucible, Sprinkle a mixture of 75g ferric oxide powder and 220g aluminum oxide powder above the pretreated vanadium pentoxide particles, and then spread a layer of 0.55cm thick magnesium powder above the mixture; , insert a 7cm magnesium strip into the magnesium powder, ignite the magnesium strip and slowly feed nitrogen into the crucible at the same time, control the rate of nitrogen
PUM
Property | Measurement | Unit |
---|---|---|
Density | aaaaa | aaaaa |
Density | aaaaa | aaaaa |
Density | aaaaa | aaaaa |
Abstract
Description
Claims
Application Information
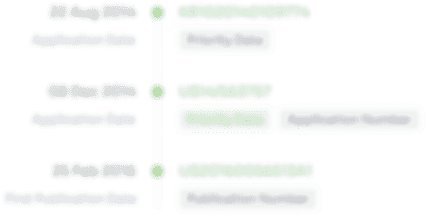
- R&D Engineer
- R&D Manager
- IP Professional
- Industry Leading Data Capabilities
- Powerful AI technology
- Patent DNA Extraction
Browse by: Latest US Patents, China's latest patents, Technical Efficacy Thesaurus, Application Domain, Technology Topic.
© 2024 PatSnap. All rights reserved.Legal|Privacy policy|Modern Slavery Act Transparency Statement|Sitemap