Segmented heating and cooling quenching process for wheel body of thrust wheel
A technology of segmental heating and support rollers, which is applied in the direction of quenching agent, quenching device, process efficiency improvement, etc., can solve the problems of slow and uneven quenching speed of support rollers, deformation and cracking hardness, etc., achieve uniform cooling, improve The effect of induction heating speed and uniform hardness
- Summary
- Abstract
- Description
- Claims
- Application Information
AI Technical Summary
Benefits of technology
Problems solved by technology
Method used
Image
Examples
Embodiment 1
[0043] figure 1 It is the flow chart of the segmental heating, cooling and quenching process of the roller body of the present invention, consisting of figure 2 It can be seen that the segmental heating, cooling and quenching process of the roller body includes the following steps:
[0044] S1, placing and positioning the rollers: grab the rollers by the manipulator and place them on the supporting platform in the quenching device;
[0045] S2, through the induction coil body, carry out the induction heating of intermediate frequency-high frequency-intermediate frequency on the supporting wheel in sequence;
[0046] S3, cooling the track rollers after induction heating: performing water-salt water-oil spray cooling on the track rollers after induction heating in sequence.
[0047] Among them, such as figure 2 As shown, step S3 specifically includes the following steps:
[0048] S31, the induction coil body slides vertically upwards along the inner wall of the quenching devi
Embodiment 2
[0063] On the basis of Embodiment 1, this embodiment provides an implementation of step S2, such as Figure 4 As shown, step S2 specifically includes the following steps:
[0064] S21, set the induction coil body with the same shape as the track roller on the outer side of the track roller, and there is a gap between the induction coil body and the track roller, and the gap is 1 mm;
[0065] S22, the rotating shaft connected under the horizontal center of the support platform rotates to drive the support platform to rotate, and the support platform rotates to drive the rollers to rotate;
[0066] S23, the induction coil body is connected to the medium-frequency induction heating power supply through the first switch, and the supporting wheels are evenly heated to a temperature of 500°C±20°C at the same time, and kept for 20 seconds;
[0067] S24, the induction coil body is connected to the high-frequency induction heating power supply through the first transfer switch, and the s
PUM
Property | Measurement | Unit |
---|---|---|
Hardness | aaaaa | aaaaa |
Abstract
Description
Claims
Application Information
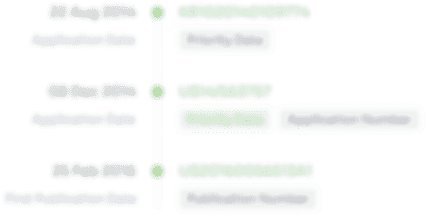
- R&D Engineer
- R&D Manager
- IP Professional
- Industry Leading Data Capabilities
- Powerful AI technology
- Patent DNA Extraction
Browse by: Latest US Patents, China's latest patents, Technical Efficacy Thesaurus, Application Domain, Technology Topic.
© 2024 PatSnap. All rights reserved.Legal|Privacy policy|Modern Slavery Act Transparency Statement|Sitemap