Method for producing concentrated nitric acid storage tank by winding carbon fibers
A concentrated nitric acid, carbon fiber technology, applied in packaging, large containers, transportation and packaging, etc., can solve the problems of self-weight, reduce the weight of the tank, and it is difficult to meet the requirements of railway transportation, and achieve the optimal winding angle and prevent galvanic corrosion. Effect
- Summary
- Abstract
- Description
- Claims
- Application Information
AI Technical Summary
Problems solved by technology
Method used
Image
Examples
Embodiment 1
[0044] This embodiment discloses a method for preparing a concentrated nitric acid storage tank by winding carbon fibers, including the following steps:
[0045] (1) According to the performance and safety requirements of the concentrated nitric acid storage tank, and according to the GB150 design standard, calculate the carbon fiber layer winding thickness. The carbon fiber layer winding thickness is 5 mm, and according to the mechanical strength of the carbon fiber material, calculate the carbon fiber layer winding at different parts of the tank The angle of winding is 15 degrees, 55 degrees, 90 degrees, and 8 layers of winding angles of 15 degrees, 20 layers of winding angles of 55 degrees, and 6 layers of winding angles of 90 degrees;
[0046] (2) Use mechanical grinding and acetone to clean the pure aluminum liner to make the surface clean;
[0047] (3) prepare the carbon fiber layer material for winding, the carbon fiber layer material is the mixture of epoxy resin and curi
Embodiment 2
[0054] This embodiment discloses a method for preparing a concentrated nitric acid storage tank by winding carbon fibers, including the following steps:
[0055] (1) According to the performance and safety requirements of the concentrated nitric acid storage tank, according to the GB150 design standard, calculate the winding thickness of the carbon fiber layer. The carbon fiber layer winding thickness is 4.5 mm. According to the mechanical strength of the carbon fiber material, calculate the carbon fiber layer winding at different parts of the tank The angle of winding is 15 degrees, 55 degrees, 90 degrees, and 9 layers of winding angles of 15 degrees, 18 layers of winding angles of 55 degrees, and 4 layers of winding angles of 90 degrees;
[0056] (2) Use mechanical grinding and acetone to clean the pure aluminum liner to make the surface clean;
[0057] (3) prepare the carbon fiber layer material for winding, the carbon fiber layer material is the mixture of epoxy resin and cur
Embodiment 3
[0064] This embodiment discloses a method for preparing a concentrated nitric acid storage tank by winding carbon fibers, including the following steps:
[0065] (1) According to the performance and safety requirements of the concentrated nitric acid storage tank, according to the GB150 design standard, calculate the winding thickness of the carbon fiber layer. The thickness of the carbon fiber layer is 5 mm. According to the mechanical strength of the carbon fiber material, calculate the carbon fiber layer winding at different parts of the tank The angle of winding is 15 degrees, 55 degrees, 90 degrees, and 10 layers of winding angles of 15 degrees, 20 layers of winding angles of 55 degrees, and 8 layers of winding angles of 90 degrees;
[0066] (2) Use mechanical grinding and acetone to clean the pure aluminum liner to make the surface clean;
[0067] (3) prepare the carbon fiber layer material for winding, the carbon fiber layer material is the mixture of epoxy resin and curin
PUM
Property | Measurement | Unit |
---|---|---|
Winding angle | aaaaa | aaaaa |
Winding angle | aaaaa | aaaaa |
Winding angle | aaaaa | aaaaa |
Abstract
Description
Claims
Application Information
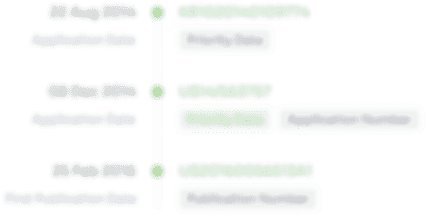
- R&D Engineer
- R&D Manager
- IP Professional
- Industry Leading Data Capabilities
- Powerful AI technology
- Patent DNA Extraction
Browse by: Latest US Patents, China's latest patents, Technical Efficacy Thesaurus, Application Domain, Technology Topic.
© 2024 PatSnap. All rights reserved.Legal|Privacy policy|Modern Slavery Act Transparency Statement|Sitemap