Plastic cavity structure of steam boiler
A steam oven and cavity technology, applied in the field of steam ovens, can solve the problems of weakened metal corrosion resistance, food safety discount, and increased installation complexity, and achieve good airtightness, safety assurance, and better effect Effect
- Summary
- Abstract
- Description
- Claims
- Application Information
AI Technical Summary
Problems solved by technology
Method used
Image
Examples
Embodiment Construction
[0020] The present invention will be further described below in conjunction with the accompanying drawings and embodiments.
[0021] see Figure 1-Figure 4 , a plastic cavity structure of a steam oven, comprising a cavity 1; the cavity 1 is composed of a panel 1.1, a side panel 1.2, a rear panel 1.3, a top panel 1.4 and a bottom panel 1.5; the panel 1.1 is provided with a cavity inlet 1.6, a cavity 1 It is one-piece injection molding of high temperature resistant plastic.
[0022] The side plate 1.2 is provided with a plurality of strip-shaped protrusions 1.21; the strip-shaped protrusions 1.21 are evenly distributed on the two side plates 1.2 in the transverse direction, and are used to support cooking utensils such as grid racks and trays.
[0023] The chamber 1 is provided with a steam inlet 2, a steam outlet 3 and a water outlet 4; the steam inlet 2 is located at the upper corner of the rear panel 1.3; several screw columns 5 are arranged on the rear panel 1.3 and the panel
PUM
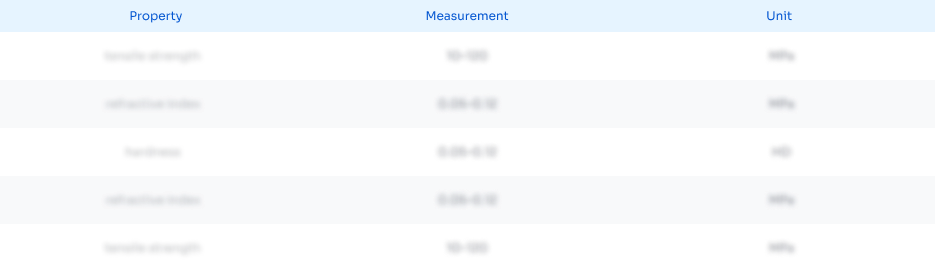
Abstract
Description
Claims
Application Information
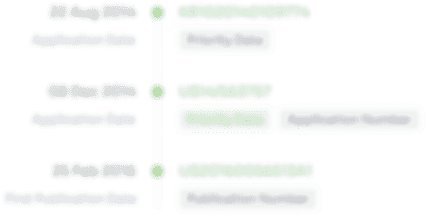
- R&D Engineer
- R&D Manager
- IP Professional
- Industry Leading Data Capabilities
- Powerful AI technology
- Patent DNA Extraction
Browse by: Latest US Patents, China's latest patents, Technical Efficacy Thesaurus, Application Domain, Technology Topic.
© 2024 PatSnap. All rights reserved.Legal|Privacy policy|Modern Slavery Act Transparency Statement|Sitemap