Lubricant for stamping die and magnesium alloy stamping molding technology
A stamping die and stamping forming technology, which is applied in the direction of lubricating composition, petroleum industry, etc., can solve the problems of affecting the service life of the mold, affecting the surface aesthetics of stamping products, and increasing the surface defects of stamping products, so as to improve the service life and reduce the cost , Improve the effect of organizational structure
- Summary
- Abstract
- Description
- Claims
- Application Information
AI Technical Summary
Problems solved by technology
Method used
Image
Examples
Example Embodiment
[0021] Example 1
[0022] A magnesium alloy stamping forming process, the specific steps are as follows:
[0023] (1) First, place a magnesium alloy thin strip (coil) material with a thickness of 0.05 mm and a width of 400 mm in a heat treatment furnace, annealed at 400 ° C for 2 hours, and heat treated before stamping;
[0024] (2) Then, after preheating the stamping die (ie, the punch and the concave die) at 290° C. for 2 hours, apply a stamping die lubricant on the stamping die;
[0025] (3) Take out the magnesium alloy thin strip (coil) material after heat treatment, place it between the preheated punch and the concave die, and stamp the magnesium alloy thin strip with a punching edge force of 6KN and a speed of 3mm / min;
[0026] (4) Finally, the formed magnesium alloy thin strip is aged at 180° C. for 25 hours to obtain a stamped product.
[0027] Wherein, the used lubricant for stamping die is composed of graphene and polytetrafluoroethylene, and the content of graphe
Example Embodiment
[0044] Example 2
[0045] The magnesium alloy stamping forming process in the present embodiment, its concrete steps are as follows:
[0046] (1) First, place a magnesium alloy thin strip (coil) material with a thickness of 0.10 mm and a width of 200 mm in a heat treatment furnace, annealed at 400 ° C for 2 hours, and heat treated before stamping;
[0047] (2) Then, after preheating the stamping die (ie, the punch and the concave die) at 260° C. for 2 hours, apply a stamping die lubricant on the stamping die;
[0048] (3) Take out the magnesium alloy thin strip (coil) material after heat treatment, place it between the preheated punch and the concave die, and stamp the magnesium alloy thin strip with a punching edge force of 5KN and a speed of 6mm / min;
[0049] (4) Finally, the formed magnesium alloy thin strip is aged at 160° C. for 30 hours to obtain a stamped product.
[0050] Wherein, the used lubricant for stamping die is composed of graphene and polytetrafluoroethylen
PUM
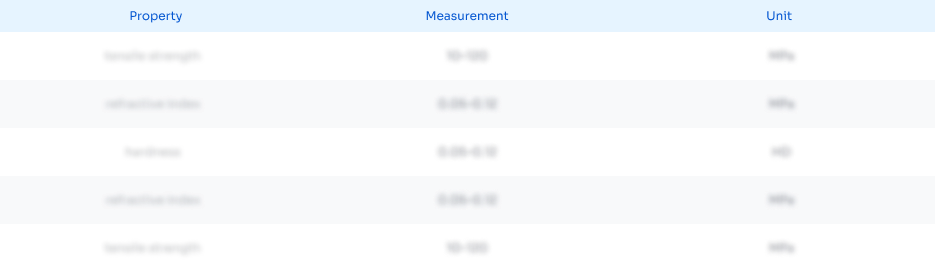
Abstract
Description
Claims
Application Information
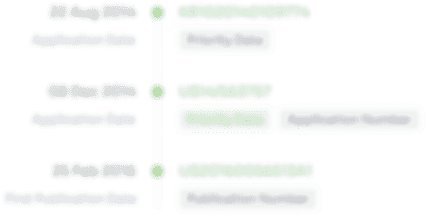
- R&D Engineer
- R&D Manager
- IP Professional
- Industry Leading Data Capabilities
- Powerful AI technology
- Patent DNA Extraction
Browse by: Latest US Patents, China's latest patents, Technical Efficacy Thesaurus, Application Domain, Technology Topic.
© 2024 PatSnap. All rights reserved.Legal|Privacy policy|Modern Slavery Act Transparency Statement|Sitemap