Preparation method of kaolin-based three-dimensional particle electrode
A particle electrode and kaolin technology, applied in chemical instruments and methods, water treatment of special compounds, water pollutants, etc., can solve the problems of application limitations, iron sludge and catalysts can not be recycled, etc., to solve the problem of troublesome operation, electrical conductivity and Good catalytic performance and the effect of increasing the reaction area
- Summary
- Abstract
- Description
- Claims
- Application Information
AI Technical Summary
Problems solved by technology
Method used
Image
Examples
Example Embodiment
[0032] Example 1
[0033] A method for preparing a kaolin-based three-dimensional particle electrode includes the following steps:
[0034] (1) Grinding: First, grind the kaolin with a ball mill, then use a mortar to grind the kaolin into a finer powder as much as possible, pass a 100-mesh molecular sieve, and place it in a constant temperature drying oven at 80°C to dry and set a constant weight; Subsequently, grind the black algae with a ball mill, and then use a mortar to grind the kaolin into a finer powder, pass 80 mesh molecular sieves, and place it in a constant temperature drying oven at 120°C to dry and set a constant weight;
[0035] (2) Mixed molding: Take 0.7446g (0.5wt% Fe) ferrous sulfate heptahydrate and 0.5859g (0.5wt% Cu) copper sulfate pentahydrate and dissolve them in 20mL deionized water, and mix the pretreated 18g kaolin powder with Put 12g of black algae powder into the mixed solution of ferrous sulfate heptahydrate and copper sulfate pentahydrate, immerse and abs
Example Embodiment
[0041] Example 2
[0042] A method for preparing a kaolin-based three-dimensional particle electrode includes the following steps:
[0043] (1) Grinding: First, grind the kaolin with a ball mill, then use a mortar to grind the kaolin into a finer powder as much as possible, pass a 100-mesh molecular sieve, and place it in a constant temperature drying oven at 100°C to dry and set a constant weight; Subsequently, grind the black algae with a ball mill, and then use a mortar to grind the kaolin into a finer powder as much as possible, pass 80 mesh molecular sieve, and place it in a constant temperature drying oven at 100°C to dry and set a constant weight;
[0044] (2) Mixed molding: Take 1.4892g (1.0wt% Fe) ferrous sulfate heptahydrate and 1.1718g (1.0wt% Cu) copper sulfate pentahydrate and dissolve them in 20mL deionized water, and dissolve 21.0g kaolin powder after pretreatment Put 9.0g of black algae powder into the mixed solution of ferrous sulfate heptahydrate and copper sulfate pe
Example Embodiment
[0050] Example 3
[0051] A method for preparing a kaolin-based three-dimensional particle electrode includes the following steps:
[0052] (1) Grinding: First, grind the kaolin with a ball mill, then use a mortar to grind the kaolin into a finer powder as much as possible, pass a 100-mesh molecular sieve, and place it in a constant temperature drying oven at 80°C to dry and set a constant weight; Subsequently, grind the black algae with a ball mill, and then use a mortar to grind the kaolin into a finer powder, pass 80 mesh molecular sieves, and place it in a constant temperature drying oven at 120°C to dry and set a constant weight;
[0053] (2) Mixed molding: take 2.9784g (2.0wt% Fe) ferrous sulfate heptahydrate and 2.3436g (2.0wt% Cu) copper sulfate pentahydrate and dissolve them in 20mL deionized water, and dissolve 24.0g kaolin powder after pretreatment Put 6.0g of black algae powder into the mixed solution of ferrous sulfate heptahydrate and copper sulfate pentahydrate, immerse
PUM
Property | Measurement | Unit |
---|---|---|
Particle size | aaaaa | aaaaa |
Abstract
Description
Claims
Application Information
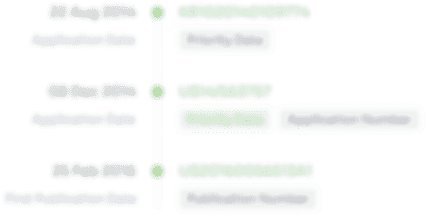
- R&D Engineer
- R&D Manager
- IP Professional
- Industry Leading Data Capabilities
- Powerful AI technology
- Patent DNA Extraction
Browse by: Latest US Patents, China's latest patents, Technical Efficacy Thesaurus, Application Domain, Technology Topic.
© 2024 PatSnap. All rights reserved.Legal|Privacy policy|Modern Slavery Act Transparency Statement|Sitemap