Method for preparing single-piece talcum powder
A talcum powder, monolithic technology, applied in the direction of magnesium silicate, silicate, etc., can solve the problems of low preparation efficiency of talc powder, inability to be widely used in the field of fillers, etc., and achieve significant market application value, high added value, and reduced production. cost effect
- Summary
- Abstract
- Description
- Claims
- Application Information
AI Technical Summary
Problems solved by technology
Method used
Examples
Embodiment 1
[0025] 1) Add 80 parts by weight of talc powder, 1 part by weight of silane coupling agent, and 0.5 parts by weight of active agent zincate into a high-speed mixer, and mix and disperse for 10 minutes at a speed of 600 rpm to obtain a premix;
[0026] 2) Add the premix obtained in step 1), 2 parts by weight of expansion agent polyethylene glycol, and 1 part by weight of blowing agent p-benzenesulfonyl hydrazide into a closed disperser, and the temperature of the disperser is controlled at 60°C to Disperse and mix at a speed of 1000rpm, turn on the vacuum negative pressure at the same time, and disperse for 20 minutes, so that the expansion agent and foaming agent are evenly dispersed in the layered structure of talcum powder to obtain an intercalation premix;
[0027] 3) Add the intercalation premix obtained in step 2) into the multi-stage disc mixer, set the speed of the multi-stage disc mixer to 600rpm, and the temperature to 120°C. The expansion agent and the foaming agent coop
Embodiment 2
[0031] 1) Add 90 parts by weight of talcum powder, 2 parts by weight of coupling agent stearate, and 0.5 parts by weight of active agent phosphate into a high-speed mixer, and mix and disperse for 5 minutes at a speed of 1200 rpm to obtain a premix;
[0032] 2) Add the premix obtained in step 1), 1 part by weight of the expansion agent sodium alginate, and 1 part by weight of the foaming agent bisbenzenesulfonyl hydrazide into the closed dispersion mixer. Disperse and mix at high speed, and at the same time turn on the vacuum negative pressure, disperse for 20 minutes, so that the expansion agent and foaming agent are evenly dispersed in the layered structure of talcum powder, and the intercalation premix is obtained;
[0033] 3) Add the intercalation premix obtained in step 2) into a multi-stage disc mixer. The multi-stage disc mixer is equipped with 2 pairs of alternate disc-type shearing elements and 2 pairs of toothed disc-type dispersing elements. , set the speed of the mu
Embodiment 3
[0037]1) Add 85 parts by weight of talc powder, 1 part by weight of silane coupling agent, and 0.5 parts by weight of active agent aluminate into a high-speed mixing mixer, and mix and disperse at a speed of 600 rpm for 10 minutes to obtain a premix;
[0038] 2) Add the premix obtained in step 1), 5 parts by weight of the expansion agent β-cyclodextrin, and 2 parts by weight of the foaming agent p-toluenesulfonyl hydrazide into the closed dispersion mixer, and the temperature of the dispersion mixer is controlled at 90 ℃, disperse and mix at a speed of 800rpm, and at the same time turn on the vacuum negative pressure, disperse for 15 minutes, so that the expansion agent and foaming agent are evenly dispersed in the layered structure of talcum powder, and the intercalation premix is obtained;
[0039] 3) Add the intercalation premix obtained in step 2) into a multi-stage disc mixer, which includes 3 pairs of disc-type shearing elements and 4 pairs of toothed disc-type dispersing
PUM
Property | Measurement | Unit |
---|---|---|
Specific surface area | aaaaa | aaaaa |
Specific surface area | aaaaa | aaaaa |
Specific surface area | aaaaa | aaaaa |
Abstract
Description
Claims
Application Information
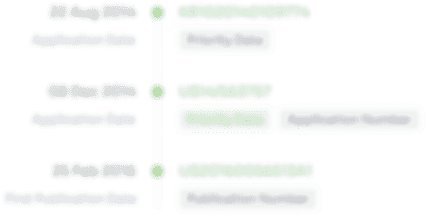
- R&D Engineer
- R&D Manager
- IP Professional
- Industry Leading Data Capabilities
- Powerful AI technology
- Patent DNA Extraction
Browse by: Latest US Patents, China's latest patents, Technical Efficacy Thesaurus, Application Domain, Technology Topic.
© 2024 PatSnap. All rights reserved.Legal|Privacy policy|Modern Slavery Act Transparency Statement|Sitemap