Artificial stone and preparation method thereof
A technology of artificial stone and slag liquid, applied in the field of artificial stone, can solve problems such as utilization, and achieve the effect of reducing the content, reducing the impact and reducing the amount of use
- Summary
- Abstract
- Description
- Claims
- Application Information
AI Technical Summary
Benefits of technology
Problems solved by technology
Method used
Image
Examples
preparation example Construction
[0026] The invention provides a method for preparing artificial stone, such as figure 1 As shown, the first coal material and the first gasification agent are gasified in the gasification unit to obtain molten slag liquid and crude gas; the molten slag liquid discharged from the gasification unit is directly cast become artificial stone.
[0027] In the present invention, the molten slag liquid is not quenched into a solid slag material and discharged from the gasification unit, but the molten slag liquid is maintained at high temperature and flowing liquid state for slag discharge, and then the molten slag liquid enters the slag It is cast into artificial stone in a liquid forming system.
[0028] According to the present invention, the method further includes: feeding dry slag powder into the gasification unit, the dry slag powder is fly ash, calcium carbide production slag, blast furnace slag and / or sulfuric acid production waste slag, the dry slag powder The melting point
Embodiment 1
[0067] This example illustrates the preparation method of the artificial stone of the present invention.
[0068] according to figure 1 The flow shown
[0069] (1) Gasification: the coal of Daliuta Mine in Shendong mining area is ground into coal material (average particle size is 0.09mm) through the coal milling unit, and the fly ash of Shenmu electric field is ground into dry slag powder (average particle size) The particle size is 0.09mm), and then respectively enter the gasification unit through the pneumatic conveying unit and contact with oxygen for gasification reaction. The total amount of coal material added is 500kg / km 3 Syngas, dry slag powder added at 100kg / km 3 For syngas, the total amount of gasification agent (oxygen) added is 350Nm 3 / km 3 Syngas, the gasification reaction temperature is 1400°C.
[0070] The gasification unit is a gasifier, such as image 3 As shown, the side wall of the gasification chamber is provided with a first nozzle for injectin
Embodiment 2
[0075] This example illustrates the preparation method of the artificial stone of the present invention.
[0076] according to figure 1 The flow shown
[0077] (1) Gasification: The coal of Bulianta Mine in Shendong Mining Area is ground into coal material (average particle size is 1 mm) through the coal grinding unit, and the sulfuric acid waste residue is ground into slag powder (average particle size is 0.1 mm) through the waste residue grinding unit mm), and then through the pneumatic conveying unit respectively into the gasification unit to contact with oxygen for gasification reaction, the total amount of coal material added is 500kg / km 3 Syngas, dry slag powder added at 100kg / km 3 For syngas, the total amount of gasification agent (oxygen) added is 400Nm 3 / km 3 Syngas, the gasification reaction temperature is 1350°C.
[0078] The gasification unit is a gasifier, such as image 3 As shown, the side wall of the gasification chamber is provided with a first nozzl
PUM
Property | Measurement | Unit |
---|---|---|
Melting point | aaaaa | aaaaa |
The average particle size | aaaaa | aaaaa |
Average compressive strength | aaaaa | aaaaa |
Abstract
Description
Claims
Application Information
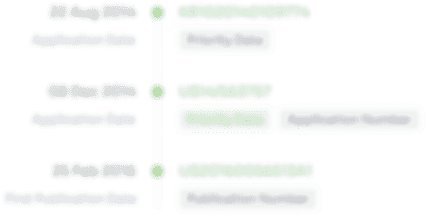
- R&D Engineer
- R&D Manager
- IP Professional
- Industry Leading Data Capabilities
- Powerful AI technology
- Patent DNA Extraction
Browse by: Latest US Patents, China's latest patents, Technical Efficacy Thesaurus, Application Domain, Technology Topic.
© 2024 PatSnap. All rights reserved.Legal|Privacy policy|Modern Slavery Act Transparency Statement|Sitemap