Composite welding method of pillow beam, pillow beam and rail vehicle with pillow beam
A hybrid welding and composite welding technology, applied in the field of rail vehicles, to achieve the effects of improving corrosion resistance, good gap adaptability, and improving manufacturing and processing efficiency
- Summary
- Abstract
- Description
- Claims
- Application Information
AI Technical Summary
Benefits of technology
Problems solved by technology
Method used
Image
Examples
Embodiment 1
[0043] Embodiment 1 proposes a corbel, such as figure 1 As shown, the corbel adopts austenitic stainless steel material SUS301L instead of weathering steel material, which realizes the lightweight of corbel and improves the corrosion resistance of corbel. The corbel includes a lower cover 3, an upper cover 1, and two side webs 9 connected between the upper cover 1 and the lower cover 3, and the two side webs 9 are respectively connected with the upper cover 1 and the lower cover The plate 3 is arranged vertically, and the lower cover plate 3, the web plates 9 on both sides and the upper cover plate 1 are welded to form a hollow box-shaped structure. The box-shaped structure is welded with ribs, which are composed of a plurality of ribs in advance. It is assembled and welded, and the assembled rib plate is formed with a plurality of plug joints 6 extending outward for subsequent plug-in operations. figure 1 In order to facilitate the display of the internal structure of the box-s
Embodiment 2
[0058] The second embodiment proposes a composite welding method for the corbel, which can be used to weld and manufacture the corbel as described in the first embodiment, so that the corbel can be made of stainless steel as a whole instead of the weathering steel material, so that the weight of the corbel can be reduced, Improve the corrosion resistance of the corbel, and have the process effect of single-sided welding and double-sided forming, which can reduce the welding deformation, solve the problem of serious residual stress, effectively improve the welding quality, and realize the maintenance-free manufacturing process of the stainless steel corbel.
[0059] like Figure 7 As shown, the method includes the following steps:
[0060] S1. Pre-assemble and weld a plurality of rib plates to form a rib plate composition, and the rib plate composition has a plurality of plug connectors 6 extending outward;
[0061] S2. Insert the lower cover 3, the two side webs 9 connected betw
Embodiment 3
[0083] On the basis of the method described in the second embodiment, the third embodiment provides a more complete example of welding processing of corbels, so as to further improve the method described in the second embodiment in detail.
[0084] In the method described in the third embodiment, according to the processing principle of first assembly and then parts, formulating the manufacturing process flow of the bolster includes in sequence: pre-assembly of the rib plate assembly, welding of the bolster, processing of the bolster, welding of the seat plate, and There are five steps in seat plate processing.
[0085] Step (1) Pre-assembly of the rib plate assembly: Use a master to connect the two ends of a pair of transverse rib plates 4 between a pair of longitudinal rib plates 5 respectively, so as to pre-assemble a rectangular structure, and then perform laser- MAG composite welding; wherein, on the basis of the length dimension of the transverse rib plate 4, a process weig
PUM
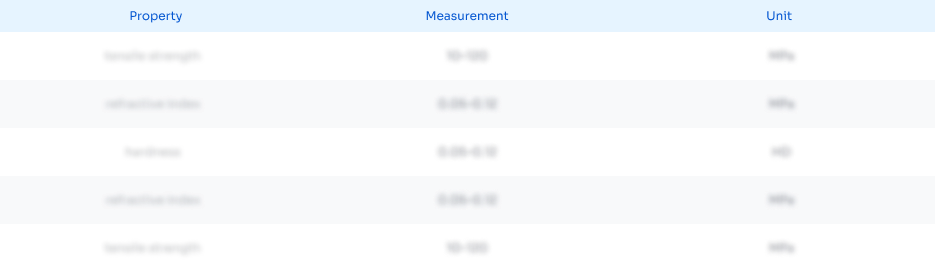
Abstract
Description
Claims
Application Information
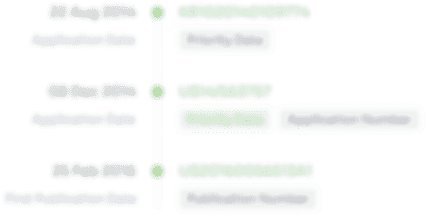
- R&D Engineer
- R&D Manager
- IP Professional
- Industry Leading Data Capabilities
- Powerful AI technology
- Patent DNA Extraction
Browse by: Latest US Patents, China's latest patents, Technical Efficacy Thesaurus, Application Domain, Technology Topic.
© 2024 PatSnap. All rights reserved.Legal|Privacy policy|Modern Slavery Act Transparency Statement|Sitemap