Full tailing glue stuff slurry and preparation method thereof
A technology for cementing filling and filling slurry, applied in sustainable waste treatment, solid waste management, climate sustainability, etc., can solve the problems of mining waste residue settlement, increase filling cost, increase operating cost, etc., and simplify the preparation process. , The effect of improving process reliability and improving work reliability
- Summary
- Abstract
- Description
- Claims
- Application Information
AI Technical Summary
Problems solved by technology
Method used
Examples
Example Embodiment
[0029] Example 1:
[0030] A full tailings cemented filler slurry is composed of cement and tailings, wherein the ratio of ash to sand is 1:4, the tailings are 20% low-concentration tailings slurry produced by beneficiation, and the prepared filler slurry has a concentration of 75%.
[0031] The preparation method of full tailings cemented filler slurry is as follows:
[0032] 1) The low-concentration tailings slurry produced by the dressing plant is thickened to 45% through a thickener, and then an alkaline medium is added to it, and the pH of the tailings slurry is adjusted to be neutral to obtain a neutral tailings slurry;
[0033] 2) Send 50% of the neutral tailings slurry to the tailings filter press system for pressure filtration treatment to obtain the filter press tailings slurry. After the press filter, the water content of the tailings slurry is 20%. The alkaline medium is preliminarily mixed with lime powder and Saturated medium made by mixing water;
[0034] 3) Feed the filter
Example Embodiment
[0036] Example 2:
[0037] A full tailings cemented filler slurry is composed of cement and tailings, wherein the ratio of ash to sand is 1:8, the tailings are 20% low-concentration tailings slurry produced by beneficiation, and the prepared filler slurry has a concentration of 80%.
[0038] The preparation method of full tailings cemented filler slurry is as follows:
[0039] 1) Pass the low-concentration tailings slurry produced by the dressing plant to 58% through a thickener, and then add alkaline medium to it to adjust the pH of the tailings slurry to neutral to obtain a neutral tailings slurry;
[0040] 2) Send 60% of the neutral tailings slurry to the tailings filter press system for pressure filtration to obtain a filter press tailing slurry. After the press filter, the water content of the tailings slurry is 14%. The alkaline medium is preliminarily mixed with lime powder and Saturated medium made by mixing water;
[0041] 3) Feed the filter press tailings slurry and the remainin
Example Embodiment
[0043] Example 3:
[0044] A full tailings cemented filler slurry, composed of cement and tailings, in which the ratio of ash to sand is 1:7.6, and the tailings are 15% low-concentration tailings slurry produced by beneficiation. The prepared filler slurry has a concentration of 75.5% .
[0045] The preparation method of full tailings cemented filler slurry is as follows:
[0046] 1) The low-concentration tailings slurry produced by the dressing plant is thickened to 57% through a thickener, and then an alkaline medium is added to it, and the pH of the tailings slurry is adjusted to be neutral to obtain a neutral tailings slurry;
[0047] 2) Send 55% of the neutral tailings slurry to the tailings filter press system for filter press treatment to obtain the filter press tailings slurry. After the press filter, the water content of the tailings slurry is 16%. The alkaline medium is preliminarily mixed with lime powder and Saturated medium made by mixing water;
[0048] 3) Feed the filter p
PUM
Property | Measurement | Unit |
---|---|---|
Strength | aaaaa | aaaaa |
Strength | aaaaa | aaaaa |
Strength | aaaaa | aaaaa |
Abstract
Description
Claims
Application Information
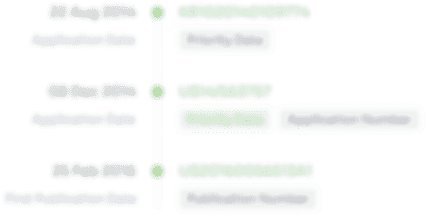
- R&D Engineer
- R&D Manager
- IP Professional
- Industry Leading Data Capabilities
- Powerful AI technology
- Patent DNA Extraction
Browse by: Latest US Patents, China's latest patents, Technical Efficacy Thesaurus, Application Domain, Technology Topic.
© 2024 PatSnap. All rights reserved.Legal|Privacy policy|Modern Slavery Act Transparency Statement|Sitemap