Composite sodium-ureido lubricating grease and preparation method thereof
A grease and urea-based technology, applied in the field of composite sodium-urea-based grease and its preparation, can solve the problems of poor mechanical stability of urea-based grease, limit the application of urea-based grease, poor adhesion, etc., and achieve excellent performance , good adhesion, and the effect of expanding the scope of application
- Summary
- Abstract
- Description
- Claims
- Application Information
AI Technical Summary
Problems solved by technology
Method used
Examples
Embodiment 1
[0023] 1. Take 50kg of mineral oil and heat it up to 80°C, divide it into two parts, add 5.4kg of p-toluidine and 2.1kg of cyclohexylamine to one part, add 8kg of 4,4-diphenylmethane diisocyanate to one part, and stir for 10 minutes respectively , the oil solution of organic amine is slowly added to the oil solution of 4,4-diphenylmethane diisocyanate for reaction, the temperature is controlled at 50-90°C, and the reaction time is 30min.
[0024] 2. Add 1kg of sodium hydroxide 10% aqueous solution to the above reaction, control the temperature at 80-100°C, and stir evenly at constant temperature.
[0025] 3. Mix 1.5kg of succinic acid and the remaining 30kg of mineral oil and add it to the reaction kettle. The temperature is controlled at about 100°C and the reaction is 60 minutes.
[0026] 4. Slowly raise the temperature for dehydration. After dehydration, the temperature rises to 180°C.
[0027] 5. When the temperature is lowered to about 90°C, add 0.5kg of diphenylamine, 0.5k
Embodiment 2
[0030] 1. Take 50kg of synthetic oil and heat it up to 80°C, divide it into two parts, add 7.5kg of cyclohexylamine to one part, add 8kg of toluene-2,4-diisocyanate to one part, stir for 10 minutes respectively, and mix the oil solution of organic amine Slowly add to the oil solution of toluene diisocyanate to react, the temperature is controlled at 50-90°C, and the reaction time is 30min.
[0031] 2. Add 1kg of sodium hydroxide 10% aqueous solution to the above reaction, control the temperature at 80-100°C, and stir evenly at constant temperature.
[0032] 3. Mix 1.5kg of acetic acid and the remaining 30kg of synthetic oil and add it to the reaction kettle. The temperature is controlled at about 100°C, and the reaction is carried out for 60 minutes.
[0033] 4. Slowly raise the temperature for dehydration. After dehydration, the temperature rises to 180°C.
[0034] 5. When the temperature is lowered to about 90°C, add 0.5kg of diphenylamine, 0.5kg of zinc dialkyldithiophosphate
Embodiment 3
[0037] 1. Take 55kg of synthetic oil and heat it up to 80°C, divide it into two parts, add 8.5kg of octadecylamine to one part, and add 5kg of toluene-2,4-diisocyanate to one part, stir for 10 minutes respectively, and slowly dissolve the oil solution of organic amine Add to the oil solution of toluene diisocyanate to react, the temperature is controlled at 50-90°C, and the reaction time is 30min.
[0038] 2. Add 1kg of sodium hydroxide 10% aqueous solution to the above reaction, control the temperature at 80-100°C, and stir evenly at constant temperature.
[0039] 3. Mix 0.5kg of acetic acid and the remaining 20kg of mineral oil and add them to the reaction kettle. The temperature is controlled at about 100°C and the reaction is for 60 minutes.
[0040] 4. Slowly raise the temperature for dehydration. After dehydration, the temperature rises to 180°C.
[0041] 5. When the temperature is lowered to about 90°C, add 0.5kg of diphenylamine, 0.5kg of zinc dialkyldithiophosphate T202
PUM
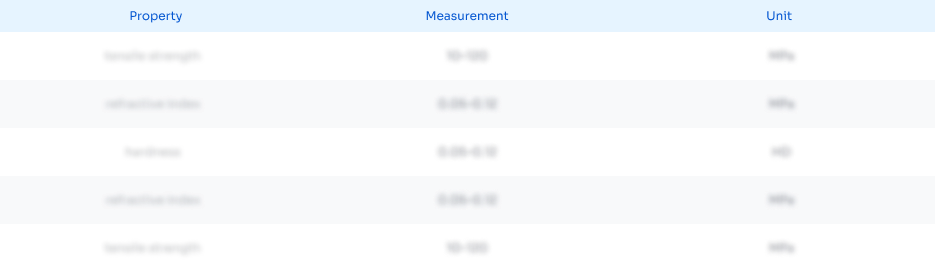
Abstract
Description
Claims
Application Information
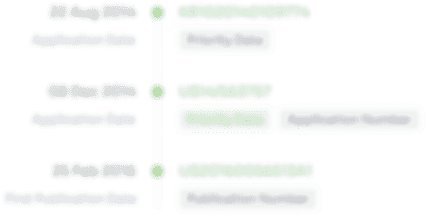
- R&D Engineer
- R&D Manager
- IP Professional
- Industry Leading Data Capabilities
- Powerful AI technology
- Patent DNA Extraction
Browse by: Latest US Patents, China's latest patents, Technical Efficacy Thesaurus, Application Domain, Technology Topic.
© 2024 PatSnap. All rights reserved.Legal|Privacy policy|Modern Slavery Act Transparency Statement|Sitemap