Method for extracting Fe from ion ore tailings
A technology for iron ore tailings and iron sand tailings, applied in chemical instruments and methods, magnetic separation, solid separation, etc., can solve problems such as technical content, long production cycle, environmental pollution, etc., to improve the level of mineral processing and Effects of economic benefit, stability of chemical composition and phase composition, high technology and economic value
- Summary
- Abstract
- Description
- Claims
- Application Information
AI Technical Summary
Benefits of technology
Problems solved by technology
Method used
Examples
Embodiment 1
[0033] 650 kg of iron ore tailings (produced by Magnetite in Panzhihua, Sichuan, containing 14% magnetite), add water to adjust to a slurry with a solid content of 60%, and then pre-enrich the iron ore through a spiral classifier. Since the specific gravity of iron ore is much greater than that of associated minerals, after the slurry is processed through the spiral classifier, the iron ore will remain at the bottom of the spiral classifier, while the associated minerals will be discharged from the top of the spiral classifier as overflow. 200 kg (dry basis) of enriched iron ore tailings were obtained.
[0034] Take 50 kg (dry basis) of enriched iron ore tailings, add water to adjust to a slurry with a solid content of 50%, and use an ultra-fine swirling mill (WXA3 type, Shenzhen Weixiong Machinery Equipment Co., Ltd.) for ultra-fine grinding. treatment, the particle size of the finished product after superfine treatment is 1250 mesh, and then sodium acrylate is added as a chemic
Embodiment 2
[0036] Get 50 kg (dry basis) of the enriched iron ore tailings in Example 1, add water and adjust to a slurry with a solid content of 50%, and use an ultrafine cyclone mill (WXA3 type, Shenzhen Weixiong Machinery Co., Ltd. company) for ultra-fine treatment, the particle size of the finished product after ultra-fine treatment is 1250 mesh, and then add sodium acrylate as a chemical auxiliary agent, the amount added is 0.33% of the pulp weight (dry basis) in the ultra-fine process, that is, 0.165 kg , carry out the reconciliation treatment, and then enter the magnetic separation in the continuous magnetic separator to obtain 7.27 kg of iron concentrate powder, which contains 92.66% of total iron after testing, and the extraction rate is 96.23%.
Embodiment 3
[0038]Get 50 kilograms (dry basis) by the enriched iron ore tailings that the method in embodiment 1 obtains, add water and adjust to the ore slurry of solid content 50%, with superfine cyclone mill (WXA3 type, Shenzhen Wei Xiong Machinery Equipment Co., Ltd.) for ultra-fine treatment, the particle size of the finished product after ultra-fine treatment is 1250 mesh, and then add sodium acrylate as a chemical auxiliary agent, the amount added is 0.8% of the pulp weight (dry basis) in the ultra-fine process , that is, 0.4 kg is reconciled, and then enters the continuous magnetic separator for magnetic separation to obtain 7.22 kg of iron concentrate powder, which contains 94.92% of total iron after testing, and the extraction rate is 97.90%.
PUM
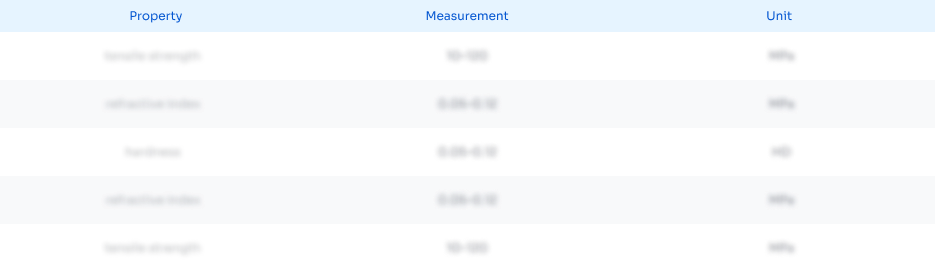
Abstract
Description
Claims
Application Information
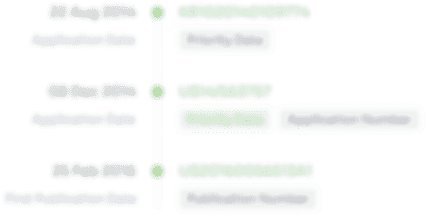
- R&D Engineer
- R&D Manager
- IP Professional
- Industry Leading Data Capabilities
- Powerful AI technology
- Patent DNA Extraction
Browse by: Latest US Patents, China's latest patents, Technical Efficacy Thesaurus, Application Domain, Technology Topic.
© 2024 PatSnap. All rights reserved.Legal|Privacy policy|Modern Slavery Act Transparency Statement|Sitemap