A method for preparing a fireproof sol polyethylene corrugated pipe
A corrugated pipe and polyethylene technology, which is applied in the field of corrugated pipes, can solve the problems of poor compatibility between flame retardants and resins, and reduce the stability and strength of finished corrugated pipes, so as to achieve good flame retardant and fireproof performance, improve mechanical properties, and good phase capacitive effect
- Summary
- Abstract
- Description
- Claims
- Application Information
AI Technical Summary
Problems solved by technology
Method used
Examples
Example Embodiment
[0020] Example 1
[0021] A preparation method of a fireproof sol polyethylene corrugated pipe includes the following steps:
[0022] (1) Take 3 parts by weight of ethylenediaminetetraacetic acid, add it to 80 times its weight in deionized water, stir evenly, add 1 part by weight of sodium carboxymethyl cellulose, and heat and stir at 50°C for 10 minutes to obtain Aqueous fiber dispersion;
[0023] (2) Take 10 parts by weight of ethyl orthosilicate and add it to the above aqueous fiber dispersion, stir evenly, add 10% ammonia water dropwise, adjust the pH to 11, stir at room temperature for 2 hours, add 0.8-1 weight Parts of coconut diethanolamide, stir evenly to obtain an amide sol dispersion;
[0024] (3) Take 3 parts by weight of ammonium polyphosphate and add it to 17-20 times its weight in deionized water, stir evenly, add 0.7 parts by weight of p-aminobenzene sulfonic acid, and heat and stir at 46°C for 3 minutes to obtain the carboxyl group Ammonium polyphosphate solution;
[002
Example Embodiment
[0029] Example 2
[0030] (1) Take 4 parts by weight of ethylenediamine tetraacetic acid, add it to 90 times its weight in deionized water, stir evenly, add 2 parts by weight of sodium carboxymethyl cellulose, and heat and stir for 20 minutes at 60°C to obtain Aqueous fiber dispersion;
[0031] (2) Take 16 parts by weight of ethyl orthosilicate and add it to the above-mentioned aqueous fiber dispersion, stir evenly, add dropwise ammonia water with a concentration of 12%, adjust the pH to 12, stir at room temperature for 3 hours, and add 01 parts by weight Coconut oleic acid diethanolamide, stir evenly to obtain an amide sol dispersion;
[0032] (3) Take 3 parts by weight of ammonium polyphosphate, add it to 20 times its weight in deionized water, stir evenly, add 0.7 parts by weight of p-aminobenzenesulfonic acid, and stir at 50°C for 7 minutes to obtain carboxyl polyphosphoric acid Ammonium solution
[0033] (4) Mix 6 parts by weight of talc powder and 1 part by weight of cyanuric chl
PUM
Property | Measurement | Unit |
---|---|---|
Tensile strength | aaaaa | aaaaa |
Ring stiffness | aaaaa | aaaaa |
Abstract
Description
Claims
Application Information
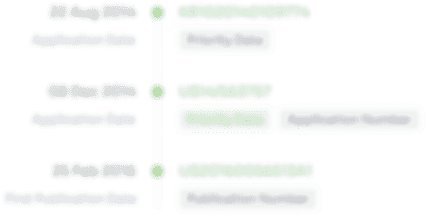
- R&D Engineer
- R&D Manager
- IP Professional
- Industry Leading Data Capabilities
- Powerful AI technology
- Patent DNA Extraction
Browse by: Latest US Patents, China's latest patents, Technical Efficacy Thesaurus, Application Domain, Technology Topic.
© 2024 PatSnap. All rights reserved.Legal|Privacy policy|Modern Slavery Act Transparency Statement|Sitemap